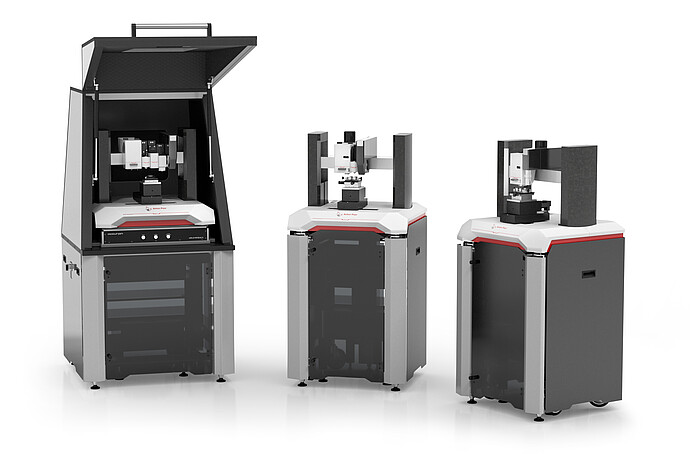
インデンテーション試験機
高精度なインデンテーション試験を幅広く実施
アントンパールのインデンテーション試験機では、薄膜、コーティング、バルク材料の硬さや弾性率などの機械的特性を正確に測定することができます。軟質、硬質、脆性、延性を問わず、ほぼすべての種類の材料に対応しています。また、ナノメートル領域での表面のクリープ、疲労、応力-ひずみ測定も可能です。
インデンテーション試験機のベースにあるのはStepプラットフォームです。Stepプラットフォームは、さまざまなタイプのインデンテーション試験機やスクラッチ試験機に対応するハウジングを備えた汎用性の高い表面試験プラットフォームで、最大4種類の試験 (インデンテーション試験、スクラッチ試験、ビッカース試験、トライボロジー試験) に対応します。
Anton Paar プロダクト
幅広い荷重レンジと試験方法
アントンパールのインデンテーション試験機のポートフォリオは、幅広い荷重レンジに対応しており、市場で最も汎用性と応用性に優れたソリューションです。ナノ/マイクロ/ビッカース硬さ試験に対応した試験機により、金属、セラミック、半導体、ポリマーなど、数え切れないほどの材料の試験が可能ですさらにワンステップ進んだ試験をご希望であれば、インデンテーション試験機にスクラッチ試験用ヘッドを組み合わせ、1台の試験機で最大4種類の試験法を実施することができます。
インデンテーション試験
インデンテーション試験では、硬さ、弾性率、クリープなど、材料の機械特性を評価することができます。試験中は、荷重と深さが連続的にモニタリングされて、荷重と深さの関係を示す曲線がディスプレイに表示されます。
独自の試料表面の検知システム
アントンパールのインデンテーション試験機が同種の他社製品と一線を画す設計上の特徴は、独自の試料表面の検知システムです。当社の装置の設計には、インデンテーション圧子とは別に試料表面を検知する圧子が付属しており、押し込み深さの基準となります。
高いフレーム剛性
アントンパール独自の試料表面の検知システムにより、インデンテーション試験のフレーム距離は最小限に抑えられ、最高のフレーム剛性を実現し、瞬時に高精度の測定結果を得ることができます。
簡単なサンプルナビゲーションで時間を節約
インデンテーション試験機は、高倍率対物レンズとサイドビューカメラを組み合わせた独自のデュアルビュー顕微鏡を搭載しています。そのため、簡単なマウススクロール操作で、サンプル表面の広い視野から最高倍率 (10,000倍) までのシームレスな移行が可能です。
ウェブセミナー
製品、アプリケーション、科学的なトピックに関するライブのウェブセミナーや記録を提供しています。
もっと見る