Inline Density Meter:
L-Dens
- Entry-level models with 1 kg/m³ accuracy
- Excellent price-performance ratio
- All-in-one instrument in a compact design
- Works even for aggressive liquids
The L-Dens inline density meters are more than just state-of-the-art measuring instruments – they’re the result of over 40 years of practical experience in process density measurement. The L-Dens 7000 series combines high accuracy and a compact design, making it the first choice for precise density and concentration measurements. Thanks to the modular system and the wide range of integration options, these instruments can be easily integrated into measurement systems or production equipment.
The L-Dens 3300 inline density meters are budget-friendly entry-level models. The instruments are designed as a stand-alone unit, so there are no additional costs.
Key features
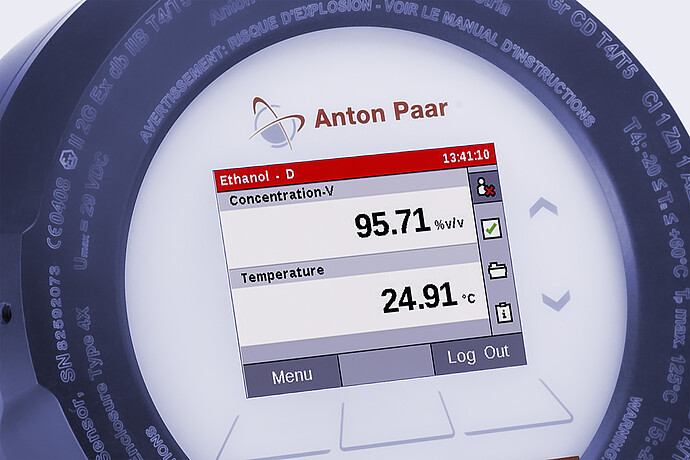
Accurate and reliable even under changing process conditions
- Get highly accurate density and concentration measurements with a compact design
- Use the most powerful inline density meter series in its class
- Ensure high product quality, optimize energy and raw material consumption, and maximize production capacity
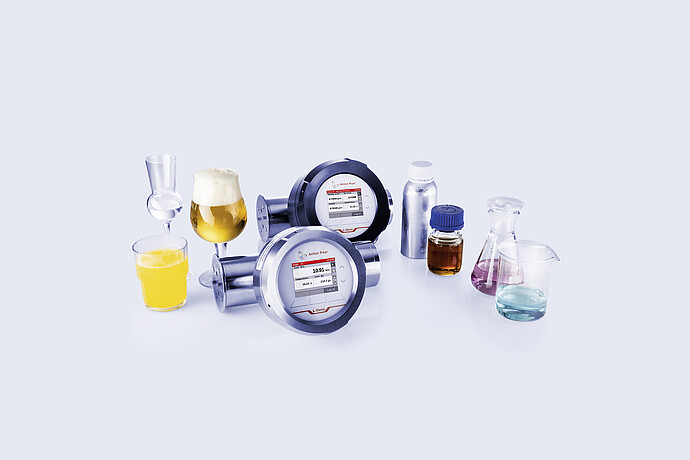
Inline density meters, optimized for every industry
- Use the instruments, which are built with different oscillator materials, to measure non-corrosive and aggressive liquids, even in hazardous environments
- Meet the requirements of a wide variety of applications in virtually all industries, including the chemical, beverage, petroleum, pharmaceutical, and ethanol industries
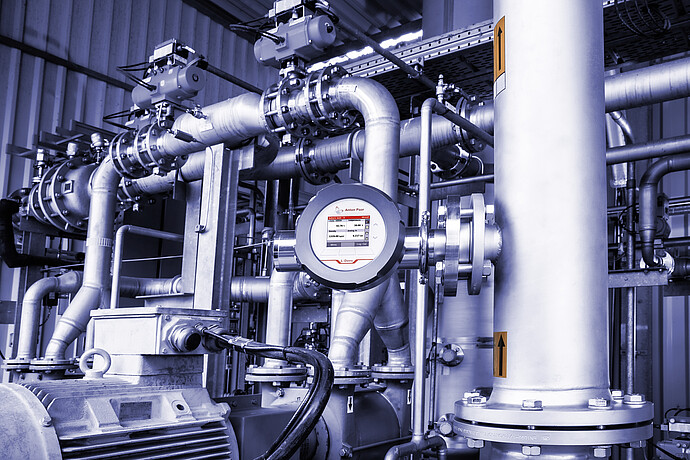
Maintenance-free, minimal integration costs
- Use inline density meters that don’t need maintenance or consumables
- Adapt the modular instruments to your respective installation requirements, and keep your integration costs low
- Access a range of Anton Paar accessories for inline, bypass, or tank installation
- Benefit from small pumps that have been integrated into the instrument. These are controlled by the density meter, which means extremely fluctuating flow rates – or tank installation – pose no problem
- Use these integrated pumps in hazardous areas with our new Inline Pump 300 Ex d
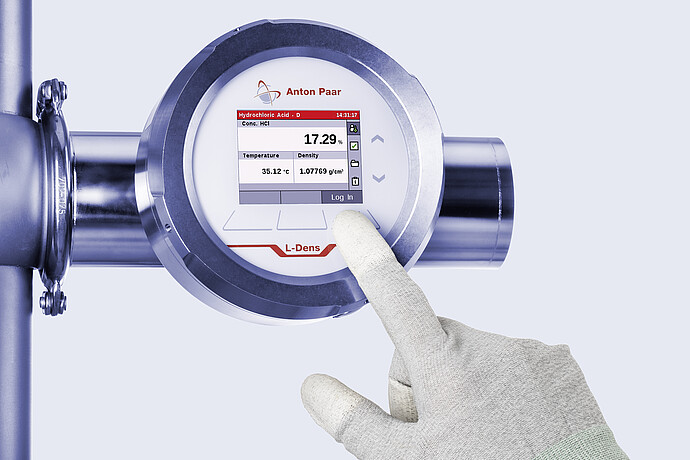
Easy to commission, easy to operate
- Connect the inline density meters to the powerful mPDS 5 evaluation unit or combine them with the smart transmitter Pico 3000
- Access a variety of communication protocols depending on your requirements
- Get started quickly: instruments arrive factory-adjusted and preconfigured so you get correct instrument settings and application formulas from the get-go
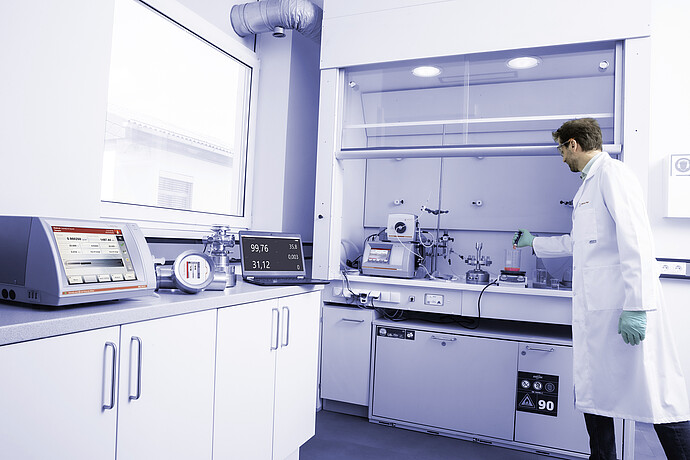
Comprehensive application know-how
- Rely on our comprehensive database to help you best measure the concentration of your liquid
- Draw on our industry expertise:
- If your application isn’t in our database, we’ll develop a formula just for you
- We’ll suggest the measuring method (density, sound velocity, or refractive index) that’s most suitable for your concentration measurement
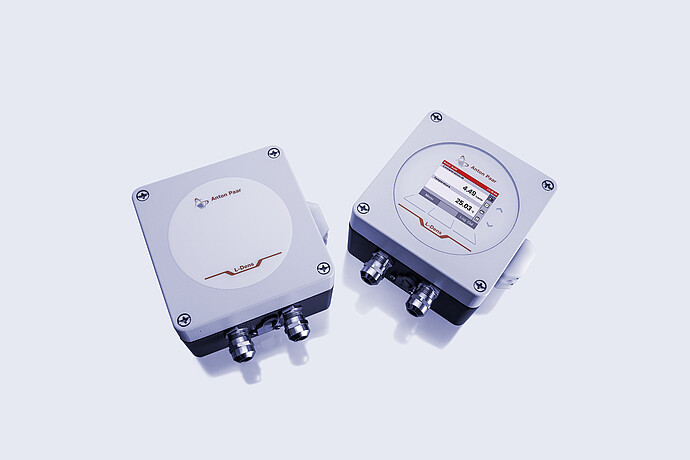
L-Dens 3300: An entry-level model for all industries
- Get 3-digit accuracy at an excellent price-performance ratio with these inline density meters
- Stay flexible with integrated applications
- Measure non-corrosive liquids, like cleaning fluids, as well as aggressive liquids, such as sulfuric acid, with a stainless steel or glass oscillator
- Use the L-Dens 3300 in every industry
Technical specifications
L-Dens 3300 | L-Dens 7300 Petro | L-Dens 7400 | L-Dens 7500 | |
U-tube inner diameter | SST: 2.1 mm GLS: 2.0 mm | 6.3 mm | ||
Density range | 500 kg/m³ to 2000 kg/m³ | Max. 1500 kg/m³ | Max. 3000 kg/m³ | Max. 2000 kg/m³ |
Standard adjustment range | 500 kg/m³ to 2000 kg/m³ | 600 kg/m³ to 1200 kg/m³ | ||
Material of the wetted parts | SST: 1.4571, 1.4404, PVDF, Viton® GLS: Glass, PVDF, Kalrez® | 1.4404 | 1.4404 Alloy C-276 Incoloy 825 Tantalum | Alloy C-276 |
Accuracy in the adjusted range | 1 kg/m³ | 0.5 kg/m³ | 0.1 kg/m³ Tantalum: 0.5 kg/m³ | 0.05 kg/m³ |
Process temperature | SST: 10 °C to +80 °C (95 °C for 30 min.) GLS: -10 °C to +60 °C | -40 °C to +125 °C (145 °C for max. 30 min.) | ||
Ambient temperature (non-Ex versions) | 10 °C to 40 °C | -40 °C to +70 °C | ||
Process pressure absolute | SST: max. 16 bar GLS: max. 6 bar | Max. 50 bar | Max. 50 bar | Max. 50 bar |
Recommended flow rate | SST: 10 L/h to 80 L/h GLS: 10 L/h to 70 L/h | 100 L/h to 500 L/h | ||
Communication | Analog, RS-232, RS-485, Relay | Can be combined with Pico 3000, Pico 3000 RC and mPDS 5 | ||
Process connections | G 1/8” | Adapters for inline, bypass, and tank installation Flange: EN, ANSI, JIS, Tri-Clamp, Varivent®; G 3/8”, Tube OD 12 mm or 1/4”; others on request | ||
Ex-Version | - | ATEX, IECEx, cQPSus, INMETRO, Peso | ||
Dimensions: non-Ex version (L x W x H) Ex version (L x W x H) | 166 mm x 155 mm x 91 mm - | - 245 mm x 160 mm x 205 mm | 245 mm x 145 mm x 185 mm 245 mm x 160 mm x 205 mm | 190 mm x 145 mm x 185 mm 190 mm x 160 mm x 205 mm |
Standards
ASTM
OIML
Anton Paar Certified Service
- More than 350 manufacturer-certified technical experts worldwide
- Qualified support in your local language
- Protection for your investment throughout its lifecycle
- 3-year warranty
Documents
-
Beverage | Beer | Complete your Beer Analysis Application Reports
-
Beverage | Soft Drinks | Online Process Measurement in the Soft Drink Industry Application Reports
-
Beverage | Spirits | Complete your Spirits Analysis Application Reports
-
Beverage | Spirits | Is your spirit safe? Application Reports
-
Beverage | Wine | Complete your wine analysis Application Reports
-
Chemistry | Automatic product identification during unloading Application Reports
-
Chemistry | CH2O | Online measurement of formaldehyde and methanol concentration Application Reports
-
Chemistry | CMP: Slurry Measurements Application Reports
-
Chemistry | Concentration Measurement Application Reports
-
Chemistry | H2SO4 | Lead-Acid Battery Production Application Reports
-
Chemistry | H2SO4 | Monitoring Pickling Baths Application Reports
Similar products
Accessories
Accessories
Accessories
Accessories
If you do not find the item you require, please contact your Anton Paar sales representative.
To find out if you can purchase online from your location, check the online availability below.
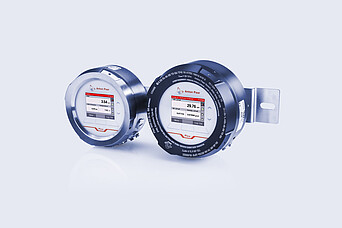
High-Performance Transmitter:
Pico 3000
L-Dens 3300 | 7300 Petro | 7400 | 7500
- High-performance transmitter for real-time measurement
- Integration into the sensor or as a separate remote-control unit
- Various analog/digital and fieldbus interfaces
- Optional Product Selection Mode: Define up to 32 products
- Free Pico 3000 configuration software
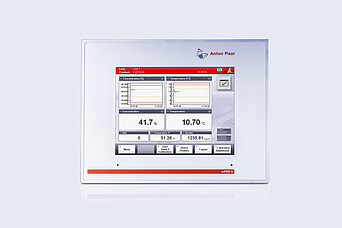
Evaluation Unit:
mPDS 5
L-Dens 3300 | 7300 Petro | 7400 | 7500
- Preconfigured user programs
- Enhanced usability with intuitive human-machine interface
- Alerts to prevent out-of-spec production
- Flexible connectivity and access with different user levels