Lithium-Ion Batteries
Research, development, and utilization of lithium-ion batteries is one of the fastest-growing industrial segments in the world. Numerous products, including pacemakers, drones, cars, and now even airplanes, rely on batteries for power. Ensuring batteries are safe, powerful, and reliable is more critical than ever before.
However, the safety, performance, and lifetime of a battery will only be as good as the materials that go into making it. Specifically, the electrodes, separator, and electrolyte need to be fully characterized and monitored from the time they enter the production facility until they are incorporated into the final product.
Parameters that have to be measured include: electrode surface area, crystal structure, particle and crystallite size, pore size, electrode slurry flow and curing properties, chemical purity of raw materials, separator pore size and structure properties, electrolyte viscosity, density, and flash point.
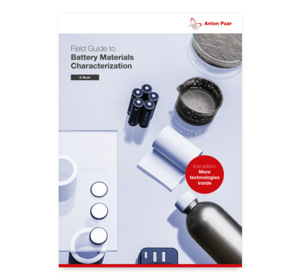
The must-read Anton Paar e-book: “Field guide to battery materials characterization”
Great battery materials power top-performing batteries. This e-book, containing real measurement data, tells you how to characterize essential lithium-ion battery materials across electrodes, slurries, separators, and electrolytes – so your batteries outperform the competition.
Let’s Talk Batteries the Anton Paar Way
Battery Experts with Anton Paar provides an overview of the most common characterization techniques used in the R&D and manufacturing of lithium-ion batteries. In this video series, an Anton Paar batteries expert will cover a range of topics relating to how to characterize the physical properties of battery materials during manufacturing.
In this video, we will discuss sample preparation for elemental composition and trace metal analysis of battery materials.
For all components used in battery manufacturing, it is crucial to accurately measure the exact elemental composition of these materials and the presence of trace contaminants, as this will have a direct impact not only on the performance of the battery, but also on its safety.
That’s where microwaves digestion systems come in, to help with sample preparation for further analysis.
Solid electrode material
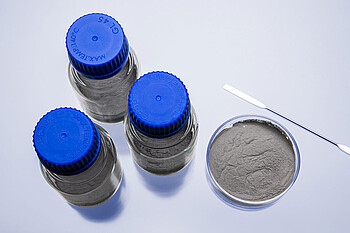
The electrodes (cathodes and anodes) of lithium-ion batteries play a key role in the transfer of ions, and are therefore crucial for efficient energy transfer. These electrodes consist of compacted particulate materials. Both the chemical composition and the physical characteristics of these materials will critically influence the battery’s performance, lifecycle, and safety, which in turn will guide design optimization of the battery for its intended use.
Physical properties of the electrode material, such as the surface area, particle size, crystallite size and shape, and pore size, have a direct effect on the charge exchange within a single cell. Other physical attributes, such as crystal structure, solid and skeletal densities, and zeta potential of electrode material particles, play a key role in the battery’s internal conductivity. And the durability of the battery will be correlated not only to the quality of the electrode coating, but to its adhesion to the electrode itself. This can be accurately assessed via quantifiable scratch testing.
Another key step in developing electrode materials is to test for heavy metal contamination. Microwave acid digestion is the initial sample preparation step for heavy metal analysis.
With methods such as XRD or SAXS, it is also possible to characterize properties of electrode materials in operando in complete battery assemblies in order to monitor changes during the charging and discharging process.
Electrode slurries
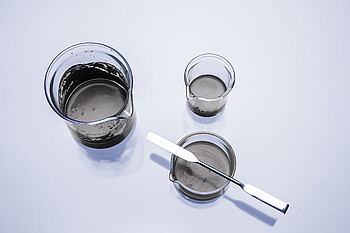
Proper design and development of the mixing and coating processes of the anode and cathode slurry is one essential part of battery performance. Knowing parameters like density, viscosity, viscoelasticity, and thixotropic behavior of the slurry provides information to determine and control composition and consistency. During mixing, unneeded agitation can thus be avoided by determining the time, speed, and temperature required to reach homogeneity. When it comes to choosing an appropriate pump or adjusting the formulation for better pumpability, the shear-rate-dependent viscosities and yield point have to be investigated. Good surface leveling during the coating process can be monitored by measuring the structural recovery.
Slurry that is being stored should not sediment out and should keep its homogeneity, which is acquired via viscoelasticity tests and zeta potential measurements. Moreover, the surface area of the slurry particles is directly related to its formulation and behavior, and knowing this parameter helps reduce material costs and ensure consistent quality.
Separators and current collectors
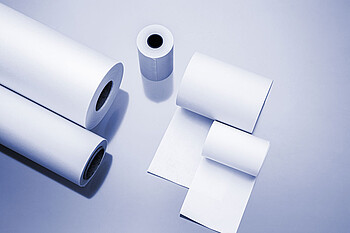
The separator in a lithium-ion battery is a thin porous membrane that plays a key role in battery function by preventing a short circuit between the anode and cathode while at the same time allowing ion flow between them. Separators need to be mechanically robust, stable under active battery conditions, and inert to other cell materials – but still be porous enough to enable ion transport.
The through-pore size of the separator is a key parameter for ensuring optimal battery performance. The pores must be small enough to prevent dendrites from forming across the separator and causing a short circuit but large enough to facilitate ion flow between the cathode and anode. Additionally, larger pores or pin holes must be screened for and prevented because they may lead to short circuits.
Another key parameter for separators is their mechanical strength and structural properties. Specifically, measuring how much pre-tension of the separator is required is key to avoiding rupture or tearing during assembly as well as sagging after assembly.
Electrolytes
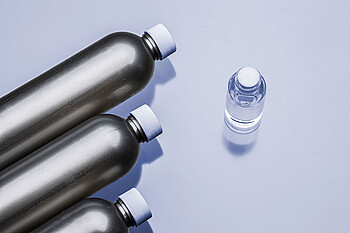
The electrolyte in lithium-ion batteries plays a key role in battery function by enabling charge transfer between the anode and cathode. The electrolyte also stabilizes cathode and anode surfaces and extends the battery lifespan. Thoroughly characterizing the physical properties of the electrolyte, specifically the density and viscosity, are crucial to ensuring conductivity, proper wetting, and filling.
The viscosity of an electrolyte solution plays a critical role in the battery’s power output, as well as in optimizing the filling process into the battery. Electrolyte solvent quality, as well as salt dissolution and concentration, are also key factors in battery performance. Density and refractive index measurements of an electrolyte solution are a fast and accurate quality control method for ensuring proper solvent quality as well as salt dissolution and concentration.
Another critical aspect of lithium-ion electrolytes is their flash point; accurately measuring this parameter is key to ensuring the thermal safety of batteries.
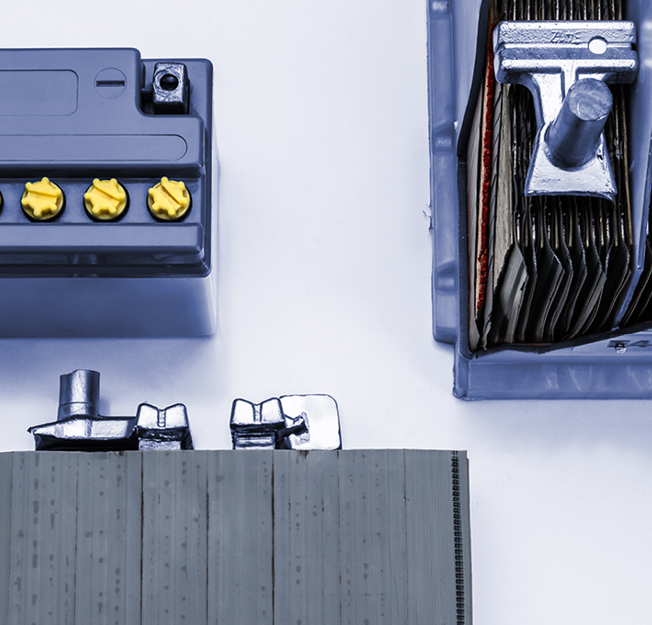
Lead-acid battery manufacturing and maintenance
Whether you are producing, maintaining, or servicing lead-acid batteries, you want to know the concentration of sulfuric acid in the battery and therefore the state of charge.
Hydrogen fuel cell production and research
To achieve the best fuel cell performance you need to understand the physicochemical properties of your active components and engineer them to your advantage. Anton Paar has the technology you need to optimize each component.
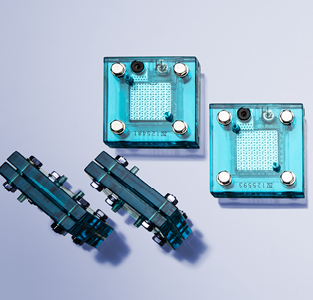