Particle Characterization
The better you understand your particles, the more accurately you can predict and optimize your materials' behavior. In today’s competitive landscape, precise particle characterization of critical parameters is essential for achieving superior results.
Anton Paar offers the most comprehensive particle characterization portfolio available from a single provider worldwide. Whichever industry you’re in, our advanced particle characterization instruments enable precise measurement of the parameters you need to refine and perfect your materials.
Particle Characterization Solutions
Instrument | Measurement | Technology | ||
---|---|---|---|---|
![]() |
|
Surface Area, Pore Size |
Pore Size Range 0.35 nm to 500 nm
BET surface area Absolute detection limit: 0.1 m² (N2 77K) Specific detection limit: 0.01 m²/g (N2 77K) Active area Absolute detection limit: 0.03 m² (H2 on Platinum 313 K) Specific detection limit: 0.003 m²/g (H2 on Platinum 313K) |
|
![]() |
|
(Bulk) Density, Powder Flow Properties | ||
![]() |
|
Reactive Area | ||
![]() |
|
Sample Preparation | ||
![]() |
|
Gas storage capacity | ||
![]() |
|
Particle Size, Particle Shape |
Particle Size Range
0.5 µm – 16,000 µm |
|
![]() |
|
Particle Size |
Particle Size Range
0.3 nm to 10 µm |
|
![]() |
|
Particle Size, Zeta Potential |
Particle Size Range
0.3 nm to 12 µm |
|
![]() |
|
Particle Size, Zeta Potential |
Particle Size Range
0.3 nm to 12 µm |
|
![]() |
|
Powder Flow Properties, Envelope Density |
Particle Size Range
5 nm to 5 mm |
|
![]() |
|
Powder Flow Properties, Density | ||
![]() |
|
Surface Area, Pore Size |
Pore Size Range
0.35 nm to 500 nm (diameter), 1.1 nm to 500 nm (with N2), 0.35 nm to 1.1 nm (with CO₂), Minimum Measurable Surface Area 0.01 m²/g |
|
![]() |
|
Pore Size |
Volume Range
0.05 cc Pore Size Range 1100 µm to 0.0064 µm |
|
![]() |
Litesizer DIF 500
Show product details
Make a request |
|
Particle Size |
Particle Size Range
0.01 µm to 3,500 µm |
![]() |
|
Particle Size, Particle Shape and Internal Structure |
Particle Size Range / Pore Size Range
< 1 nm to 105 nm (q range (Cu K-alpha): 0.03 nm⁻¹ to 41 nm⁻¹) |
|
![]() |
SAXSpoint 500 and 700
Show product details
Make a request |
|
Particle Size, Particle Shape and Internal Structure |
Particle Size Range / Pore Size Range
< 1 nm to > 300 nm (q range (Cu K-alpha): 0.01 nm⁻¹ to 41 nm⁻¹) |
![]() |
|
(True) Density |
4 cm³ to 135 cm³
|
|
![]() |
|
(True) Density |
4 cm³ to 135 cm³
|
|
![]() |
|
(Open) Cell Content |
4 cm³ to 135 cm³
|
|
![]() |
|
(True) Density |
0.25 cm³ to 4.5 cm³
|
|
![]() |
|
Particle Size, Phase Purity, Crystal Structure |
Crystallite size 5 nm to 500 nm
Phase fractions >0.1% |
What is Particle Characterization and Why is it Important?
Particle characterization plays a central role in meeting industry standards and ensuring absolute safety and reliability – whether you’re in the food, pharmaceutical, or building industries.
Anton Paar offers a range of particle characterization devices that enable precise measurement of particle size, pore size, particle shape, internal structure, zeta potential, surface area, reactive area, and much more.
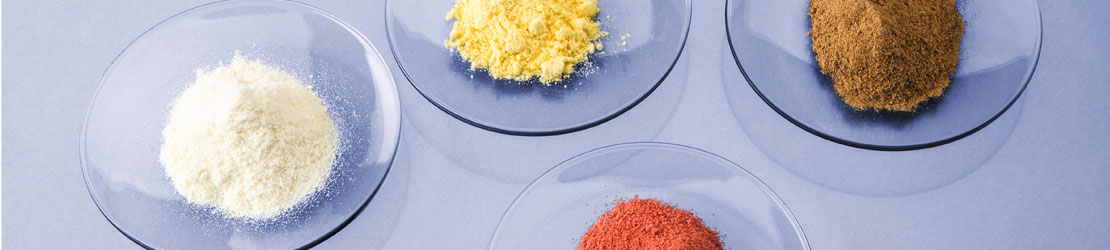
What is Particle Characterization?
Particles refer to solid, liquid, or even gas-based materials that range in size from nanometers to millimeters. Through the characterization process critical properties can be identified, such as:
Size and distribution: Understanding how particles vary in size and are distributed within a substance can affect properties like flow, reactivity, and overall product stability.
Shape: The geometry of a particle can influence how it behaves in different conditions – affecting product performance in applications such as coatings, catalysts, and pharmaceuticals.
Surface area: The amount of surface exposed impacts how particles interact both with each other and with other substances. This is especially important for processes like dissolution, reactivity, and absorption.
Zeta potential: As a measure of surface charge, this can predict particle stability in suspension, which is crucial in colloid chemistry and the formulation of suspensions.
Porosity: This determines how a particle absorbs liquids or gases, impacting sectors like filtration and catalysis.
What Are the Different Types of Particle Characterization?
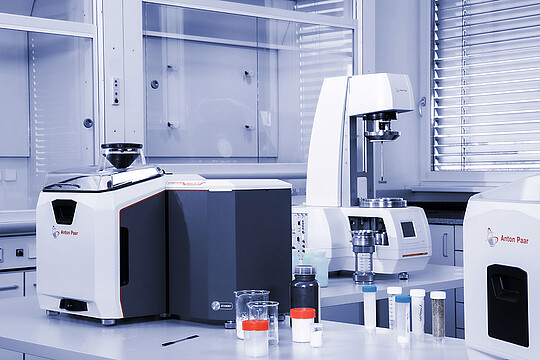
Particle characterization involves the use of a range of analytical techniques to understand and quantify the physical properties of particles in a material. Each method offers unique insights that are essential for optimizing product quality, performance, and safety across various industries – from pharmaceuticals to cosmetics and advanced materials.
The primary types of particle characterization are listed below.
1. Particle size analysis
One of the most fundamental measurements, particle size analysis, determines the distribution of particles within a sample. This is crucial for understanding how particles behave in production and application processes. Common methods include laser diffraction, dynamic light scattering (DLS), and sieving.
2. Particle shape and morphology
Particle shape influences material properties such as flow, packing, and surface area. Understanding shape is particularly important in industries like pharmaceuticals, where the morphology of active ingredients can affect drug solubility and bioavailability. Techniques include imaging techniques (optical microscopy, SEM) and automated image analysis.
3. Surface area and porosity analysis
For particles where surface interactions are key – such as catalysts, adsorbents, or pharmaceuticals – surface area and porosity are important parameters. BET surface area analysis is a key method for measuring these.
4. Zeta potential analysis
Zeta potential measures the electrical charge on the surface of particles, which directly affects their stability in suspension. This is critical in formulating products like emulsions, suspensions, and coatings. Techniques include electrophoretic light scattering (ELS).
5. Solid density analysis
Understanding solid density helps in determining how particles will behave in a given medium, especially for suspensions and emulsions. Methods include gas pycnometry and tapped density analysis.
6. Powder flow and rheology
For industries dealing with bulk powders – such as pharmaceuticals, chemicals, and food – the flow properties of a powder can significantly impact production. Particle size, shape, and surface texture all contribute to how powders behave during processing. Powder flow analyzers are particularly useful for this kind of analysis.
When Should You Use Particle Characterization?

Here are some key scenarios where particle characterization is indispensable:
1. Product development and innovation
Understanding the behavior and properties of particles in your materials during the research and development phase helps create products that meet desired specifications. Particle size, shape, surface area, and porosity all influence how your materials will perform – from pharmaceuticals to advanced composites.
2. Quality control and consistency
For manufacturers, maintaining product consistency across batches is critical. Even small variations in particle properties can lead to significant differences in product performance, stability, or shelf life.
3. Process optimization
In many industries – from food production to pharmaceuticals – the flowability, solubility, and compressibility of powders and particles can greatly affect manufacturing processes.
4. Troubleshooting and problem solving
When issues arise in production or product performance, particle characterization can help identify the root cause such as inconsistencies in particle size, changes in zeta potential, and how surface area or porosity may be influencing adsorption.
5. Regulatory compliance
Many industries are subject to strict regulatory requirements regarding the physical properties of materials. In pharmaceuticals, for example, the size, shape, and surface area of active ingredients can affect drug bioavailability and efficacy.
6. Environmental and safety considerations
Particle characterization can effectively monitor air quality, assess the safety of nanoparticles used in cosmetics or industrial applications, and control dust hazards in industries like mining, construction, or agriculture – ensuring that materials are safe for workers, consumers, and the environment.
Why Particle Characterization with Anton Paar?
As broad as Anton Paar’s particle characterization portfolio is, all of its instruments have one thing in common: market-leading quality.
Our dedicated team of scientists develop particle characterization solutions in close cooperation with users, resulting in the best possible solutions for measuring porous materials and powders.
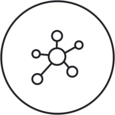
Industry Leader
As the experts in particle characterization since the middle of the 20th century, Anton Paar’s solutions continue to pave the way for reliable, accurate, and traceable measurement.
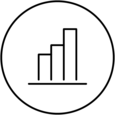
Measure Multiple Parameters
Investigate particle size, pore size, particle shape, internal structure, zeta potential, surface area, reactive area, density, powder flow, phase purity, and much more.
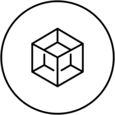
Instrument Portfolio from One Provider
Anton Paar offers the broadest particle characterization portfolio available from a single provider worldwide. Benefit from our decades of expertise in the field and enjoy the convenience of working with one trusted point of contact for all your measurement needs.
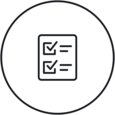
Three-Year Warranty
All Anton Paar’s particle characterization instruments include free repair for three years after purchase, providing protection from unforeseen costs. Be safe in the knowledge that worldwide support is available whenever you need it.
Particle Characterization Applications
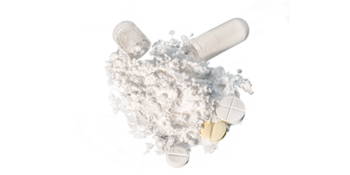
Granulation and Drying: The Challenges of Tableting
Tablets consist of active pharmaceutical ingredients (API) and excipients that enhance powder processing and dosage form quality – both of which depend on proper instrument parameters and powder handling during the granulation and drying process.
This report examines the moisture uptake capacity of milled and sieved lactose and methylcellulose to predict their behavior during wet granulation. These excipients were also tested at different temperatures to simulate fluidized bed dryer effects. Results showed that moisture adsorption during granulation and subsequent drying influence flow and compression characteristics of the powders.
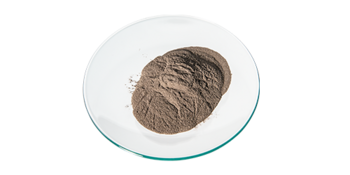
Catalyst Characterization
Characterization of catalysts, both prior to reaction and in their spent form, can provide valuable information about the effectiveness and efficiency of the catalytic process and guide the design of future catalysts. The most important parameters in this context are pore size, pore volume, active surface area, particle size, surface acidity, fluidization behavior, and cohesion properties.
Download this application report to learn how insights into all these parameters – derived from experiments using Anton Paar particle characterization instruments – contribute to catalyst development and quality control.
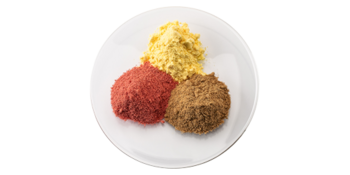
Food Characterization
Food powder formulation, manufacturing, and packaging processes require batch-to-batch consistency to ensure consumer safety and loyalty. Insights derived from experimentation using Anton Paar particle characterization instruments that determine density, particle size, cohesion strength, compressibility, and permeability can contribute to food powder quality and consistency.
This application report focuses on milk powder and all-purpose flour, which are ubiquitous products on their own and crucial ingredients in many other food products and nutritional supplements.
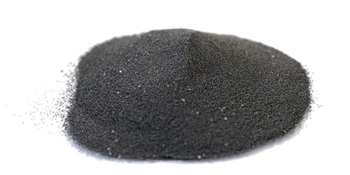
Metal Powder Characterization
Metal powders are essential in powder metallurgy operations like additive manufacturing, where their properties ensure high product quality. Common analysis methods include powder rheometry, dynamic light scattering, BET, and density measurement.
This report explains how these complementary methods assess flow properties, porosity, compressibility, packing density, and size distribution. By characterizing metal powders using these particle characterization instruments, you can ensure smooth flow during production, maintain stability in sintered products, and determine whether excess powder from previous batches remains usable.
Deep-Dive into Particle Characterization
Upgrade your particle characterization capabilities for a durable system built for the future.