Multiparameter Measurement System:
Packaged Beer Measurement Systems
- Safeguard filler performance and final product specifications
- Measure 50+ quality parameters, including total package oxygen
- Obtain all data at the push of a button in a single data set
- System is 9x quicker than conventional methods
- DMA 5001, TPO 5000, Alcolyzer 3001 Beer, Haze 3001, pH 3201, CarboQC ME
Anton Paar’s Packaged Beer Measurement Systems are single lab systems designed to swiftly analyze your final beer’s specification. Our market-leading instruments cover the entire beer industry: We offer solutions to customers ranging from craft breweries to the largest players of the industry, all of whom are committed to the consistent quality of their products, providing the most comprehensive measurement system. All systems deliver automated analysis suited to the individual requirements in just three minutes – up to nine times faster than conventional methods.
Included products
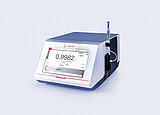
DMA 5001
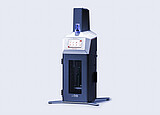
TPO 5000
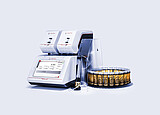
Alcolyzer Module 3001 Beer
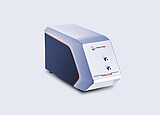
Haze 3001

pH 3101
Key features
Final quality assurance in 3 minutes
Fortify your production control with confidence in the final product: The Packaged Beer Measurement system measures all key parameters directly from the final package. Rely on batch-to-batch consistency at the storage tank already and confirm after bottling to conform with legal requirements. Immediately detect performance issues at the filler and optimize your filling process. The simultaneous analysis of all quality parameters with a single Packaged Beer Measurement system reduces analysis time to just three minutes – over nine times quicker than conventional methods.

Selective alcohol and CO₂ determination
The Packaged Beer Measurement system unites unique measuring principles for alcohol and CO2. Selectively determine alcohol content with Anton Paar's market-leading Alcolyzer and selectively measure CO2 without influence from other sample ingredients. The system delivers certainty on tax declarations based on alcohol or CO2 levels, and enables you to nail down the CO2 concentration for each of your beer styles and thrill your customers with an unmatched taste experience – all without the need for sample preparation.

Zero sample preparation
The direct, pressurized filling of a sample in a Packaged Beer Measurement system eliminates the need for sample preparation, use of glassware, and potential contamination of the product. It eliminates operator interaction with the sample and ensures airtight reliability of analysis results. The final package – either a can, glass bottle or PET bottle – is placed into the PFD filling device for direct sample transfer. The system handles any package closure type.

Easy calibration and product-independent adjustment
The system is simply calibrated and adjusted with water and a binary solution. Fully automated instructions lead you through the calibration and adjustment procedure. The superior density meter ensures complete traceability of the sample filling and measurement process through FillingCheck™ and U-View™. New recipes aren’t a challenge: All samples are measured straight away, with no need for any product-specific calibrations.

Individual system setup, with upgrade possibility
The modular setup of the Packaged Beer Measurement system lets you configure your ideal measurement solution, including all the parameters you need. Analyze all required quality parameters from a single sample on a single system in a single measurement cycle and minimize complexity in your laboratory.

World’s best beer analyzing system: Beer measurement including TPO analysis
An integrated TPO 5000 total package oxygen meter is the high-end solution for quality control of beer. It measures more than 50 quality parameters from a single package and delivers all parameters at the push of a button in a single data set. An automated leak test, combined with O2 performance verification and automatic cleaning routines, guarantees the highest efficiency in final quality control and frees up operator capacities. Easily switch between different package types – the system automatically centers your package before piercing. Cans are easily analyzed upside-down, entirely eliminating any risk of leaks during the piercing process.

Specifications
Recomended Configuration | 1 | 2 | 3 |
Parameters |
|
|
|
MEASURING RANGE | |||
Alcohol | 0 % v/v to 12 % v/v | ||
Density | 0 g/cm³ to 3 g/cm³ | ||
Original extract | 0 °Plato to 30 °Plato | ||
Color | 0 EBC to 120 EBC (0 ASBC to 60.96 ASBC) | ||
pH value | pH 0 to pH 14 | ||
Turbidity | 0 EBC to 100 EBC (0 ASBC to 6900 ASBC) | ||
CO2 concentration | 0 vol. to 5.5 vol. (0 to 11 g/L) at 35 °C (95°F), 0 vol. to 10 vol. (0 to 20 g/L) < 10 °C (50 °F) | ||
O2 concentration | DO: 0 ppm to 2 ppm HSO: 0 hPa to 45 hPa | DO: 0 ppm to 4 ppm | |
REPEATABILITY, S.D. | |||
Alcohol | 0.01 % v/v | 0.05 % v/v | |
Density | 0.000001 g/cm³ | 0.000005 g/cm³ | 0.00001 g/cm³ |
Original extract | 0.03 °Plato | 0.01 °Plato | |
Real extract | < 0.01 % w/w | 0.015 % w/w | 0.025 % w/w |
Color | 0.1 EBC (0.05 ASBC) | ||
pH value | 0.02 in the range pH 3 to pH 7 | ||
Turbidity | 0.3 % of the measured value + 0.02 EBC / 1.4 ASBC according to formazine reference suspension | ||
CO2 concentration | 0.005 vol. (0.01 g/L)* | 0.025 vol. (0.05 g/L) | |
O2 concentration | TPO: ±8 ppb or ±6 %, whichever is higher** | DO: 2 ppb (below 200 ppb) | |
ADDITIONAL INFORMATION | |||
Power features | U-View™, FillingCheck™, ThermoBalance™, full-range viscosity correction, ultra-fast measuring mode | ||
Minimum amount of sample per measurement | 260 mL | 150 mL | 30 mL |
Typical measurement time per sample | 8 minutes (incl. filling) to 10 minutes | 3 minutes (incl. filling) | |
Sample throughput | 7 samples per hour | 15 samples per hour | |
Dimensions (L x W x H) | 515 mm x 1200 mm x 1120 mm (20.3 in x 47.3 in x 44.1 in) | 482 mm x 750 mm x 670 mm (19.0 in x 29.5 in x 26.4 in) | 482 mm x 730 mm x 446 mm (19.0 in x 28.7 in x 17.6 in) |
Power supply | AC 100 V to 240 V, 50/60 Hz, fluctuation ±10 %, 190 VA | ||
Ambient temperature | 15 °C to 32 °C (59 °F to 89.6 °F) | ||
Air humidity | non-condensing 20 °C: <90% relative humidity; 25 °C: <60% relative humidity; 30 °C: <45% relative humidity | ||
STANDARDS | |||
MEBAK | Chapter 2.9.6.3 (B-590.10.181) Chapter 2.12.2 (B-420.01.272) Chapter 2.14.1.2 (B-420.01.271) | Chapter 2.9.6.3 (B-590.10.181) Chapter 2.12.2 (B-420.01.272) | |
TTB | Density measurement in proofing alcohol for tax purposes | ||
GB | T 4928-2008 | ||
EBC | Chapter 8.2.2, Chapter 9.2.6, Chapter 9.43.2, Chapter 8.5, Chapter 8.6 | Chapter 8.2.2, Chapter 9.2.6, Chapter 9.43.2 | |
BCOJ | 8.3.6 Alcolyzer for alcohol contents 8.4.3 Alcolyzer for real extract Analytical method for beer | ||
ASBC | Beer-4G: Near-infrared and original extract content (2004) | ||
AOAC | Method 956.02 (430 nm) |
* Due to sample handling and preparation in TPO 5000, CO2 mean values may deviate by 1 % absolute compared to filling by a PFD (piercing
and filling device)
** At ambient and sample temperature of 23 °C (73.4 °F) if standard cleaning is applied. Please note that the first measurement of a set is not
considered for the determination of the repeatability of a set.
Note: For information about tested package sizes please see the TPO 5000 instruction manual or contact your Anton Paar representative.
Standards
AOAC
ASBC
BCOJ
EBC
GB
Mebak
Standards
AOAC
ASBC
BCOJ
EBC
GB
Mebak
Standards
AOAC
ASBC
BCOJ
EBC
GB
Mebak
Anton Paar Certified Service
- More than 350 manufacturer-certified technical experts worldwide
- Qualified support in your local language
- Protection for your investment throughout its lifecycle
- 3-year warranty
Documents
-
Beverage | Beer | Complete your Beer Analysis Application Reports
-
Cleaning recommendations for Alcolyzer Application Reports
-
Determination of alcohol content in hard seltzers Application Reports
-
Determination of the alcohol content in kombucha Application Reports
-
Mastering the fog - chill haze measurements of beer Application Reports
-
Measurement of non-alcoholic and alcohol-free beer Application Reports
-
Measurement of non-alcoholic beer (US version) Application Reports
-
Quantifying beer - calorie determinations in beer Application Reports
-
Brochure | Beer analysis overview Brochures
-
PBA 5001 Beer | SOP Manuals