Nano Scratch Tester:
NST³
- Measurement of coating adhesion and scratch resistance
- Full panorama image synchronized with all other signals such as penetration depth and friction force
- Ideal for thin coatings below 1000 nm thickness
- Force measurement up to 1000 mN
The Nano Scratch Tester (NST3) is particularly suited for characterizing the scratch resistance and adhesion of thin films and coatings with a typical thickness below 1000 nm. Analyze organic and inorganic, as well as soft and hard coatings. The unique design of the nano-scratch measurement head includes two sensors for force and depth measurements associated with a state-of-the-art piezoelectric actuator – get results in milliseconds, plus great accuracy and great flexibility.
Combine the NST3 head with another scratch or indentation testing head to fully cover the nano, micro, and macro range. The versatility of the Step platform even allows you to add an AFM to investigate surface topography.
Key features
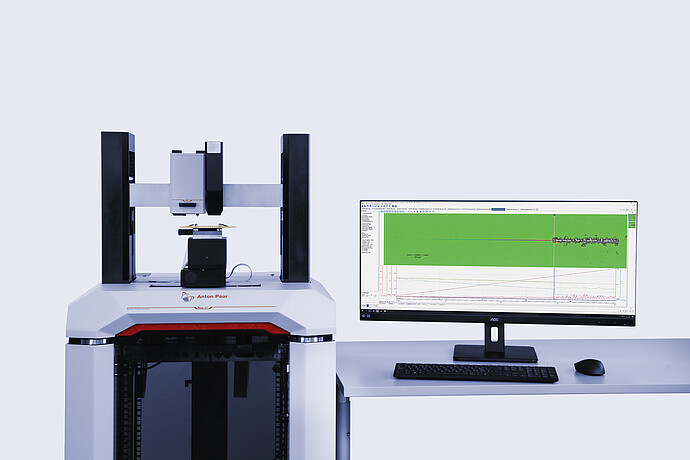
Full synchronized panorama for analysis whenever, wherever
This unique feature of our Nano Scratch Tester automatically synchronizes the panoramic image of the whole scratch in perfect focus with scratch data from all sensors. Perform critical loads analysis based on panorama observation and signal recordings at any time. Anton Paar is the exclusive holder of the synchronized panorama technique (U.S. patent 8261600 and European patent EP 2065695).
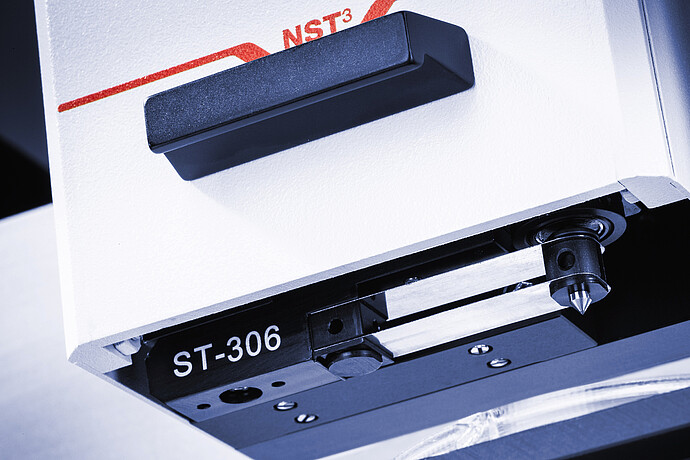
Fast small-force response
The Nano Scratch Tester incorporates a double cantilever beam for application of the load combined with a piezoelectric actuator for an ultra-fast response (within milliseconds) to the load applied. This concept also corrects the result for deviations caused by any event occurring during the scratch (e.g. appearance of cracks and failure, defects, or non-flat sample).
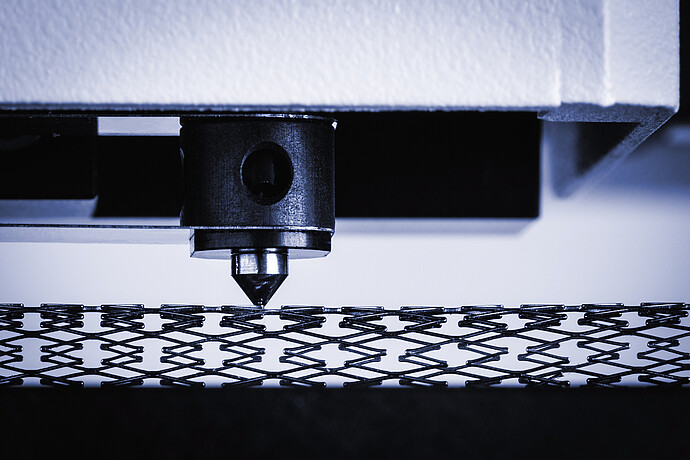
Apply exactly the force you want
The closed active force feedback loop provides even more accurate nano scratch testing (normal load resolution of 0.01 µN and noise floor of 0.1 µNm). NST³ incorporates a real sensor for force measurement that directly feeds back to the normal force actuator. This ensures reproducible scratch testing, even when you investigate more complex surface geometries like non-parallel, rough, or curved samples.
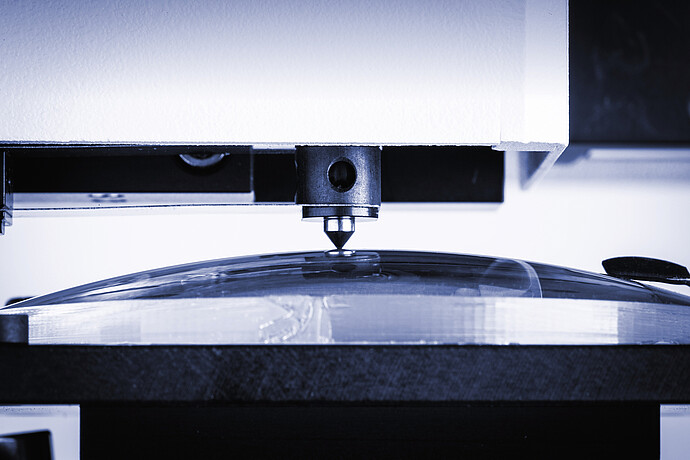
Elastic recovery studies: True penetration depth measurements
The NST³ Nano Scratch Tester incorporates a real displacement sensor for monitoring the vertical motion of the indenter. The unique technique of pre- and post-scan obtains the true depth: elastic, plastic, and viscoelastic properties of materials can therefore be evaluated. This technique involves a pre-scan recording of the surface profile (form, waviness, and roughness) of the sample before the scratch test. NST³ corrects the indenter depth during the scratch (penetration depth) and after the scratch (residual depth) using the surface profile.
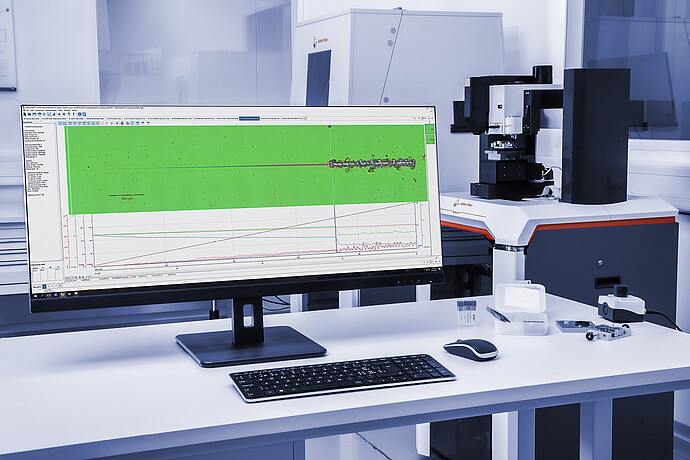
Multi-post-scan mode to measure viscous behavior after a scratch
After a scratch, you can define unlimited post-scan measurements in the software with a delta in time to measure the residual depth. This new analysis will give you additional understanding of the deformation behavior of your surface versus the recovery time.
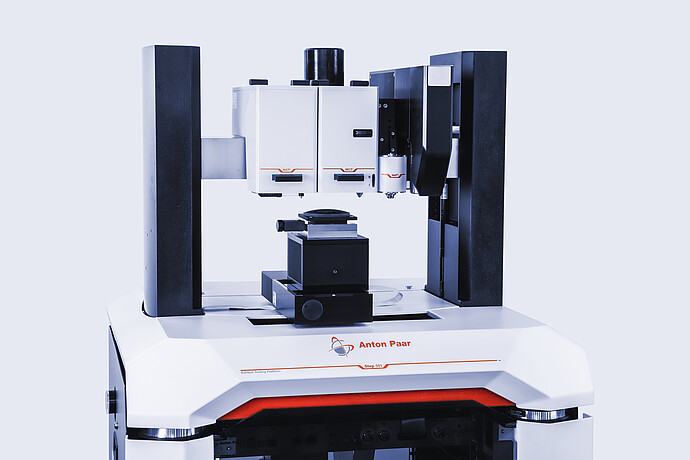
Added versatility with the Step platform
The Step platform is your all-in-one solution for surface mechanical characterization testing. Whether you want to exclusively conduct scratch tests, or enhance the results with indentation and AFM measurements, the Step platform always offers the best solution in terms of modularity, stability, and noise isolation.
Technical specifications
Maximum load [mN] | 1000 |
Load resolution [μN] | 0.01 |
Load noise floor [rms] [μN] | 0.1 |
Loading rate [N/min] | Up to 100 |
Maximum friction force [mN] | 1000 |
Friction force resolution [μN] | 1 |
Maximum depth [μm] | 600 |
Depth resolution [nm] | 0.1 |
Depth noise floor [rms] [nm] | 1.5 |
Data acquisition rate [kHz] | 192 |
Scratch speed [mm/min] | 0.1 to 600 |
Standards
ASTM
Anton Paar Certified Service
- More than 350 manufacturer-certified technical experts worldwide
- Qualified support in your local language
- Protection for your investment throughout its lifecycle
- 3-year warranty
Documents
-
Adhesion of passivation layers in semiconductor industry by nanoscratch test Application Reports
-
Applications of indentation and scratch in automotive industry Application Reports
-
Applications of scratch testing in polymer industry Application Reports
-
Biomedical applications 2: Adhesion and scratch resistance by scratch testing Application Reports
-
Characterization of hard coatings - Part I: DLC coatings Application Reports
-
Electric contact resistance (ECR) by indentation, scratch and tribology Application Reports
-
Mechanical surface characterization of smartphone displays Application Reports
-
Scratch resistance of self-healing paints on wood Application Reports
Similar products
Accessories
Accessories
Accessories
Accessories
If you do not find the item you require, please contact your Anton Paar sales representative.
To find out if you can purchase online from your location, check the online availability below.
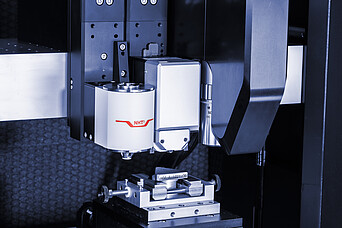
Accessory for Step Platforms:
Atomic Force Microscope (AFM)
- Versatile AFM solution for various scientific and industrial applications
- Imaging and analysis capabilities offering nanoscale surface information
- Non-destructive interaction with samples
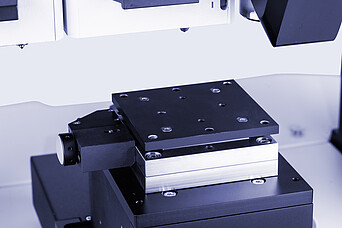
Accessory for Scratch Testers:
Friction Module
- Material’s frictional behavior assessment
- Complementary tool in the assessment of adhesion failures
- Combines scratch and tribology testing