Quality Control of Concrete
Quality control of concrete and advanced techniques for R&D are critical for ensuring consistent performance, durability, and compliance with industry standards. By analyzing, monitoring, and managing key properties like skeletal density, phase composition, and mechanical strength, manufacturers can enhance the quality and reliability of concrete across various applications.
Advanced techniques like gas pycnometry and in-situ XRD provide precise data that help refine product compositions and production processes, reduce variability, and ensure superior results.
Why Quality Control of Concrete Matters
Concrete’s performance is determined by the interaction of raw materials, mixing processes, and curing conditions. Without robust concrete quality control measures, issues such as inconsistent strength, cracking, or reduced durability can occur, leading to increased costs and potential structural risks.
Key objectives of concrete quality control include:
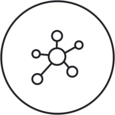
Ensuring Structural Integrity
Reliable concrete resists mechanical and environmental stresses, extending the life of structures.
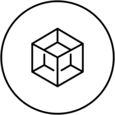
Reducing Variability
Quality control helps achieve consistent material performance across production batches.
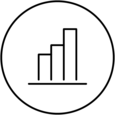
Optimizing Costs
Detecting and addressing inconsistencies early reduces waste and minimizes rework.
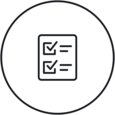
Meeting Industry Standards
Adhering to ASTM, EN, and other recognized standards ensures compliance and reliability.
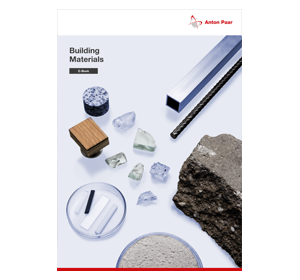
The Must-Read Anton Paar E-Book: “Building Better: A Practical Guide for Great Building Materials
Download our essential e-book for professionals in the construction and building materials industry. As the sector evolves towards more sustainable and efficient practices, this guide provides detailed insights into the characterization and improvement of key building materials, including cement, concrete, metals, composites, and architectural finishes. Alongside a broad focus on optimizing materials such as metals and composites, the e-book includes a dedicated section on quality control of concrete, exploring techniques, standards, and case studies to ensure durability, strength, and long-term performance.
Advanced Methods for Quality Control of Concrete
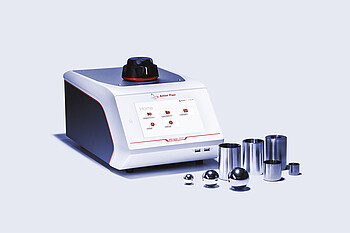
Skeletal Density Analysis
Skeletal density measures the density of the solid material in concrete, excluding pores and voids. It is a key indicator of the compactness of raw materials and the final product, making it essential for quality control of concrete.
- Gas pycnometry: This method uses gas to determine the true density of a concrete sample, enabling precise skeletal density calculations. It can detect variations in raw material quality or inconsistencies in the mixing process.
- Applications: Skeletal density analysis ensures consistent mechanical performance and strength across production batches. By monitoring this parameter, manufacturers can validate mix designs and improve overall quality assurance.
- Relevant standards:
- BS EN 12390-7: Testing Hardened Concrete – Density of Hardened Concrete
- ASTM C642: Standard Test Method for Density, Absorption, and Voids in Hardened Concrete
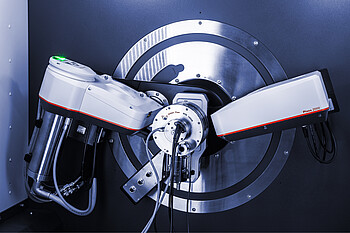
Phase Composition Analysis with In-Situ XRD
The phase composition of concrete significantly impacts its mechanical and thermal properties – both critical aspects of quality control of concrete. For materials like Autoclaved Aerated Concrete (AAC), controlling the formation of phases such as tobermorite is crucial for achieving the desired strength and insulation properties.
- In-situ XRD: This technique tracks phase transformations in real-time during curing, providing data on quartz dissolution and tobermorite crystallization under controlled conditions of temperature and pressure.
- Benefits: Real-time monitoring allows manufacturers to optimize production parameters, reducing variability, and ensuring consistent material properties.
- Relevant standards:
- ASTM C1365: Standard Test Method for Determination of the Proportions of Phases in Portland Cement and Clinker Using X-Ray Powder Diffraction
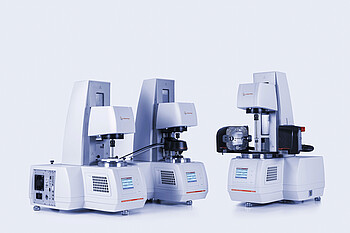
Exploring concrete rheology for high-pressure applications
Understanding the flow behavior of concrete slurries is essential for optimizing construction materials, especially in high-performance applications such as oil well cementing, deep-water construction, and CO₂ sequestration. With reduced water content, modern concrete formulations achieve superior strength and durability, but also present challenges in mixing, pumping, and workability. Rheological analysis under high-pressure conditions helps engineers develop formulations that ensure both strength and practical usability.
High-pressure rheological analysis:
This technique involves measuring the flow properties of cement slurries using a modular compact rheometer equipped with a high-pressure cell. The method assesses viscosity changes under varying pressures and shear rates, allowing engineers to observe shear thinning and thickening behaviors, which are crucial for predicting material performance in real-world conditions.
Benefits:
- Improved pumpability & workability – Understanding viscosity changes at different pressures ensures smooth mixing and application.
- Enhanced material strength – Low water-cement ratios improve durability, while rheological analysis helps fine-tune the formulation.
- Industrial applications – Supports critical applications such as oil well cementing, for which, because of extreme conditions, it is necessary to precisely determine material behavior.
Routine Property Testing
In addition to advanced analytical techniques, regular testing of properties such as compressive strength, workability, and durability is essential. These tests complement skeletal density and phase composition analyses, providing a comprehensive view of concrete quality.
Related Products
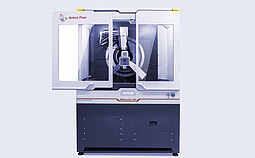
XRDynamic 500
The XRDynamic 500 delivers high-quality XRD data with fully automated optics and alignment, ideal for a range of applications from powder XRD to SAXS.
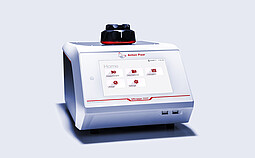
Ultrapyc
Measure density of solids and semi-solids in under 10 minutes with built-in temperature control and contamination prevention across models.
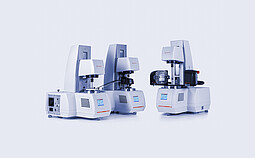
MCR 102e/302e/502e
Oscillatory and rotational rheometers from Anton Paar for QC, product development, and R&D. Choose from a wide range of application-specific accessories.
Benefits of Quality Control in Concrete Production
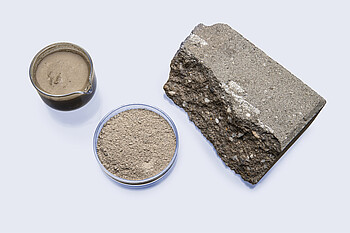
Implementing advanced quality control measures provides:
- Consistent strength and durability: Controlled skeletal density and optimized phase composition ensure reliable performance.
- Enhanced production efficiency: Early detection of inconsistencies reduces waste and prevents delays.
- Cost savings: High-quality concrete minimizes maintenance and repair costs while extending the service life of structures.
- Improved environmental impact: Optimized processes reduce material waste and energy consumption.
Contact Us to Optimize Your Concrete Quality Control