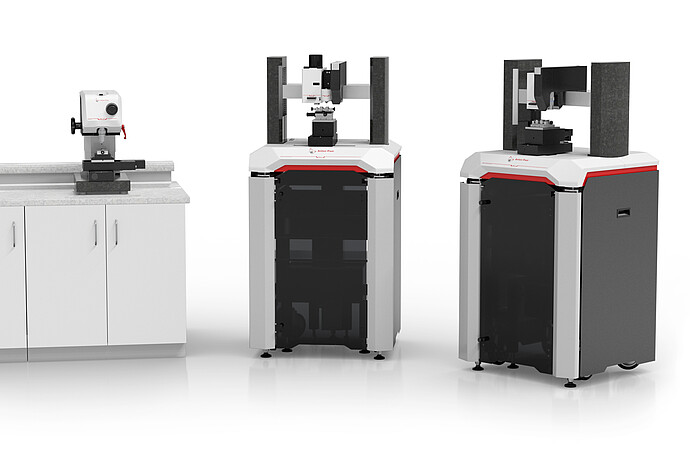
Scratch Testers
Solutions from the market leader in scratch testing
Scratch testers from Anton Paar are used to characterize film-substrate systems and to quantify properties such as adhesive and cohesive strengths, friction force, deformation, and elastic recovery, via a number of complementary methods. This makes scratch testers invaluable tools for the determination of coating adhesion, scratch, and mar resistance, in research, development, and quality control.
Scratch testers can be mounted on Step, a versatile surface testing platform that is designed to house various scratch and indentation testers. Cover up to four types of testing: instrumented indentation, scratch, automatic Vickers hardness, and basic tribology.
Anton Paar Products
Adaptable comprehensive mechanical tester
With the versatile modular Step platforms, a broad force range is covered for scratch testing, conventional hardness testing, and instrumented indentation. Seamless transitions between these methods are possible without the need for additional setups. Consolidating all three methods on one platform also ensures adaptability to future measurement needs.
Access to unique patented synchronized panorama
Anton Paar is the unique holder of the patents US 8261600 and EP 2065695. After the scratch, you can record the full panorama without loss of image resolution. The panoramic image is displayed in a perfectly synchronized way with scratch data. Once your panorama is recorded, you can re-analyze your results at any time.
More insights into true penetration depth for elastic recovery studies
The displacement sensor monitors the surface profile of your sample before, during, and after a scratch (Patent: US 6520004). This means you can evaluate the penetration depth of the indenter during and after the scratch for even more reliable insights into scratch and mar resistance.
Accurate force control even on complex surfaces
The system’s active force feedback ensures reproducible scratch testing, even when you investigate more complex surface geometries like non-parallel, rough, or curved samples. Anton Paar’s testers are the only commercially available systems that have active force feedback.
Easy sample visualization saves time
The modular scratch testers come with a dual-view microscope that combines a high-magnification objective with a side-view camera. The unique continuous zoom function allows you to find your area of interest on a large scale and zoom in to observe the details by simply scrolling through the 20x to 10000x magnification range.
Webinars
We offer you a great and constantly growing choice of live webinars and recordings on products, applications, and scientific topics.
Show more