Advanced Lubricant Analysis Solutions
Foaming gear oils, oxidized transformer fluids, inconsistent greases – lubricant issues like these cost time, money, and performance. Whether you're optimizing base oil formulations in the lab, verifying bio-lube stability, or monitoring in-service oils in real time, precise lubricant analysis is essential.
This page highlights proven test methods and trusted measurement solutions – from advanced laboratory instruments to robust inline technologies – tailored to real lubricant challenges across industries.
Why Lubricant Testing Matters
Reliable lubricant analysis helps industries run efficiently and sustainably by preventing failures, optimizing products, and meeting compliance.
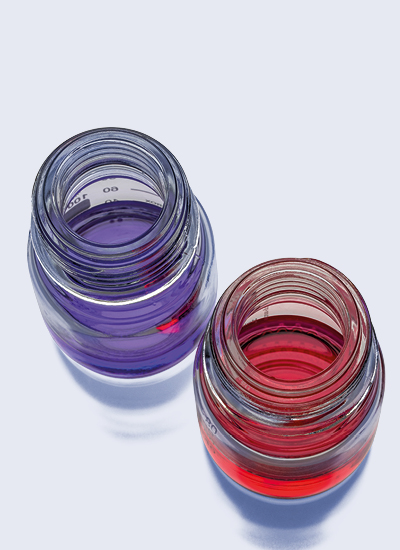
Lubricant analysis plays a vital role in extending equipment life and preventing unplanned failures. By regularly monitoring in-service oils for oxidation, wear metals, and contamination, it provides operators with deep insights into equipment health and lubricant condition, enabling precise forecasting of maintenance needs, while minimizing unexpected downtime and reducing mechanical wear. The result is longer asset life, optimized service schedules, and better use of maintenance resources – all of which contribute to substantial time and cost savings.
In standards-driven industries, lubricant testing is particularly important for ensuring compliance with international frameworks such as SAE, ASTM, ISO, and DIN. These frameworks support consistent, traceable, and comparable test results – whether you're managing lubrication across a single facility or multiple global sites. Meeting these standards allows companies to strengthen their internal quality systems, support documentation for audits, and maintain alignment with customer and regulatory expectations.
For R&D and formulation teams, lubricant analysis provides critical support in driving innovation in base oils, additive systems, and bio-lubricants. Real-world performance data allows for faster iteration, more accurate formulation adjustments, and confident validation of new lubricant technologies – whether that’s developing synthetic fluids or environmentally friendly alternatives. This enables science-based decisions that not only support faster formulation cycles and more efficient go-to-market decisions but also enhance long-term product performance.
Across production environments, lubricant analysis is equally important for optimizing operational performance and ensuring fluid reliability. Continuous monitoring of metalworking fluid quality control or transformer oil stability, for example, ensures fluids meet functional and safety standards under real-world conditions. This reduces the risk of process disruptions, protects equipment, and supports consistent, high-quality output across industrial systems.
Ultimately, lubricant analysis delivers more than just lab results – it supports smarter decision-making and long-term operational efficiency. By combining predictive insights, quality assurance, and R&D validation, it can be used as a strategic tool for improving reliability, reducing waste, and increasing profitability. In short, it helps you run cleaner, leaner, and more confidently – no matter your industry.
The Must-Read Anton Paar E-Book: Lubricant Analysis: Methods, Applications & Solutions
Gain in-depth insights into lubricant analysis across all sample types – from engine oils to food-grade lubricants. Our free e-book offers structured application know-how, recommended methods, and instrument solutions tailored to real-world workflows.
Lubricant Testing Methods
Modern lubricant testing is built on a range of standardized, application-specific methods designed to characterize essential properties such as viscosity, density, flash point, oxidation stability, and additive health.
Anton Paar supports these requirements with precision instruments tailored to laboratory and industrial needs.

Viscosity, Viscosity Index & Rheology
- What it measures: Kinematic and dynamic viscosity, temperature-dependent flow behavior, and viscosity index (VI).
- Why it matters: These properties determine lubrication film strength, pumpability, and thermal stability. They are essential for classifying oils (ISO VG, SAE grades) and understanding non-Newtonian behavior at high shear.
- Where it’s used: Gear oils, engine oils, EALs, hydraulic and transmission fluids, greases.
- Relevant standards & instruments: ASTM D7042, ASTM D445, ASTM D2270.
Density & Compositional Analysis
- What it measures: Fluid density at ambient and extreme T/p, refractive index, and molecular characteristics such as VGC and carbon-type composition.
- Why it matters: Supports formulation accuracy, base oil classification, and compliance with product specifications.
- Where it’s used: Base oils, white oils, transformer fluids, aviation lubricants.
- Relevant standards & instruments: ASTM D4052, ISO 12185, ASTM D2501, ASTM D2140.
Oxidation Stability & Flash Point Testing
- What it measures: Oxidative degradation resistance and ignition safety parameters.
- Why it matters: Through lubricant analysis, it predicts aging and assesses safe handling, contamination, and classification risks.
- Where it’s used: Engine oils, hydraulic fluids, gear oils, EALs, greases.
- Relevant standards & instruments: ASTM D8206, ISO 2719-A, ASTM D93, ASTM D942.
In-Service Oil Condition Monitoring
- What it measures: Degradation markers like soot, oxidation, additive depletion, viscosity shifts, and wear particle indicators.
- Why it matters: Enables predictive maintenance, supports extended drain intervals, and reduces operational risk.
- Where it’s used: Diesel and gasoline engines, turbines, industrial gearboxes.
- Relevant standards & instruments: ASTM D7844, ASTM D7412, ASTM D7418.
Grease Testing: Consistency, Rheology & Stability
- What it measures: Penetration (NLGI grade), high-shear behavior, oxidation stability, and tribological response under stress.
- Why it matters: Assures grease reliability in mechanical systems, bearing life, and long-term lubrication performance.
- Where it’s used: Bearings, electric motors, gear systems, e-mobility components.
- Relevant standards & instruments: DIN ISO 2137, ASTM D942, ASTM D8206.
Additive and Elemental Analysis & Bulk Fluid Handling
- What it measures: Additive concentrations, wear metals (e.g., Fe, Zn, Ca), and real-time flow/density for logistics.
- Why it matters: Ensures lubricant health, detects abnormal wear, and safeguards delivery accuracy.
- Where it’s used: Oil analysis labs, blending terminals, logistics and distribution.
- Relevant methods & instruments: ASTM D7777, ICP (via microwave digestion), L-Cor inline Coriolis mass flow.
Applications Across Lubricant Types
Our application-focused approach helps you identify key measurements for each lubricant category – ensuring targeted, efficient testing.
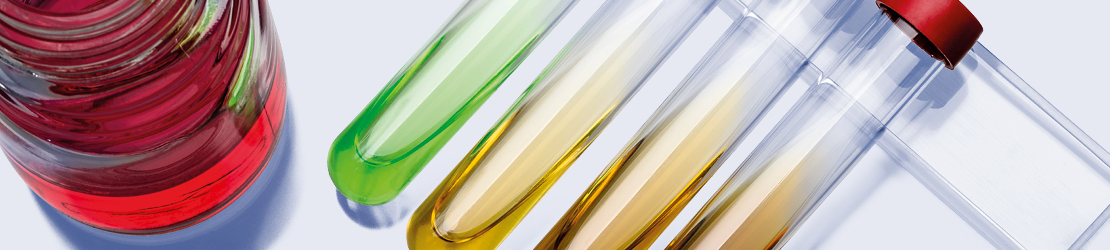
From Engines to EALs: Tailored Lubricant Analysis
Lubricating Oils
Engine, gear, base, industrial, and bio-lubricants require accurate measurement of viscosity, density, VI, and flash point to ensure reliable flow, thermal stability, and classification. These parameters are central to meeting performance standards in powertrain systems, manufacturing, and environmentally sensitive applications through accurate lubricant analysis.
In-Service/Used Oils
Used oils reveal degradation through shifts in viscosity, oxidation levels, and soot content. Tracking these changes enables early detection of equipment wear and supports maintenance scheduling based on real lubricant condition instead of fixed intervals.
Greases
Applications in EVs and industrial equipment demand high-performance greases with controlled consistency (DIN ISO 2137) and reliable rheological behavior. Friction testing and oxidation stability analysis ensure performance under mechanical stress and temperature cycling.
Metalworking & Specialty Fluids
Cutting, drawing, and grinding operations depend on emulsions and specialty fluids with tightly controlled viscosity and additive balance. Inline refractometry and viscometry help maintain fluid condition and extend tool life, particularly in automated production settings.
Hydraulic & Transmission Fluids
Fluids used in mobile machinery and aviation must perform across a broad temperature spectrum. Cold-start flowability is evaluated using ASTM D2983 and related methods, ensuring responsiveness and protection in low-temperature environments.
Specialty Lubricants and Additives
Food-grade and biodegradable lubricants must meet strict oxidative stability and compliance requirements. Meanwhile, additives – such as antiwear and friction modifiers – are assessed for their tribological impact, essential in developing high-performance, formulation-specific solutions.
Smart testing. Better lubrication. Proven results.