Fully automated sugar quality control lab:
Sugarlyzer 5000
- Fully automated factory-control lab
- Combines sample preparation, measurement and data transfer
- Cut 8 manual steps, walk away for 6 hours, process up to 300 samples a day
- Digital job management – easily adaptable to your workflow
- Planning security for your quality control workflow
Fully automated lab analysis solution for the sugar industry combining sample preparation, high-precision measurement and data transfer.
Combining multiple state-of-the-art Anton Paar instruments, the Sugarlyzer 5000 is a ready-to-use, factory-control lab that can reliably conduct all stages of the sugar analysis process. This includes the analysis of all liquid-, syrup-, molasse-like and sugar crystal samples.
Fully automated with all sample preparation steps and measurements, there's no need to train or hire specialized personnel. The Sugarlyzer 5000 oversees the execution of predefined standard operating procedures for every sample, and obtains highly precise and complete results whilst you get on with other tasks. Automation ensures increased lab efficiency, lab safety, and high repeatability and traceability of your quality control results.
Key features
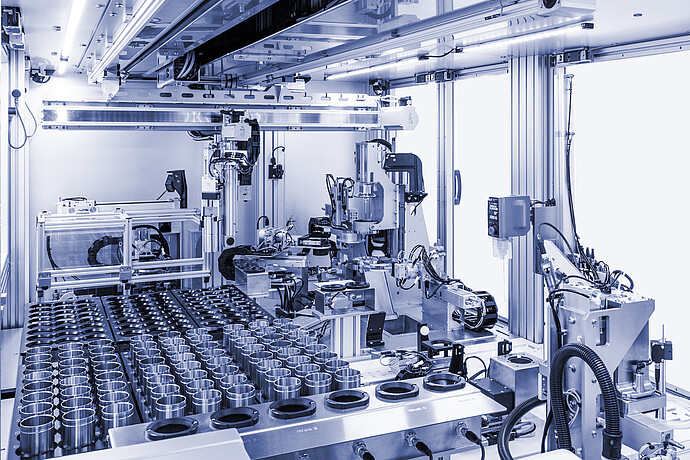
Reliable quality control for the sugar industry, fully automated
Combining sample preparation, high-precision measurement and data transfer, the Sugarlyzer 5000 subsidizes a whole lab, eliminating up to 8 manual steps with one conclusive system that mobilizes pre-defined workflows. This fully automated factory-control lab integrates measurement of all crucial parameters which are central to the sugar production process.
Enjoy all the benefits of world- class instruments including MCP 5300, DMA 4501, Haze 3001, Abbemat 650 and PH 3201 in one combined, ready-to-use lab that facilitates Anton Paar's high precision guarantee. If needed, additional instruments can be added upon customer request.
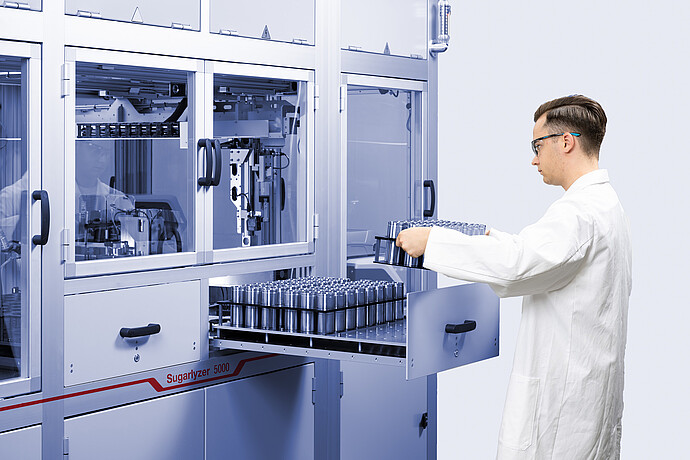
Planning security for your quality control workflows
The Sugarlzyer 5000 offers the swiftest shift to automated lab analysis in the sugar industry. It ensures the reliable processing of samples 24 hours a day, including sample preparation and measurement. Process up to 300 samples per day without obtaining skilled workers or training manual laborers to manage complex equipment. The Sugarlyzer 5000 achieves maximum productivity by working on up to 5 samples at the same time.
This is complemented further by the addition of stainless-steel cups that are automatically cleaned, produce minimal waste and guarantee longevity.
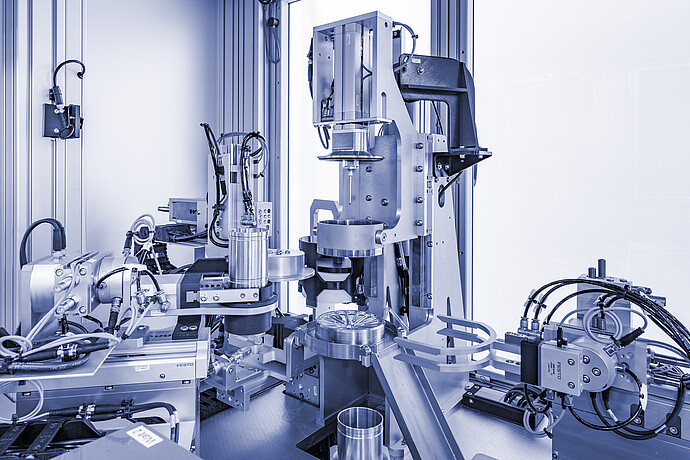
Free up time and resources
Automated sample preparation frees up time and resources by leaving the Sugarlyzer 5000 to autonomously prepare, process and clean samples. It even executes these workflow steps in parallel for multiple samples at the same time. Eliminate the need for constant management and observance of samples as the Sugarlyzer 5000 mobilizes all repetitive tasks according to your requirements.
The Sugarlyzer 5000 is equipped with extensive storage to free up users for more than 6 hours, allowing them to get on with other important tasks. Even when the results are available, there is no need to intervene as the combined data is exported automatically.
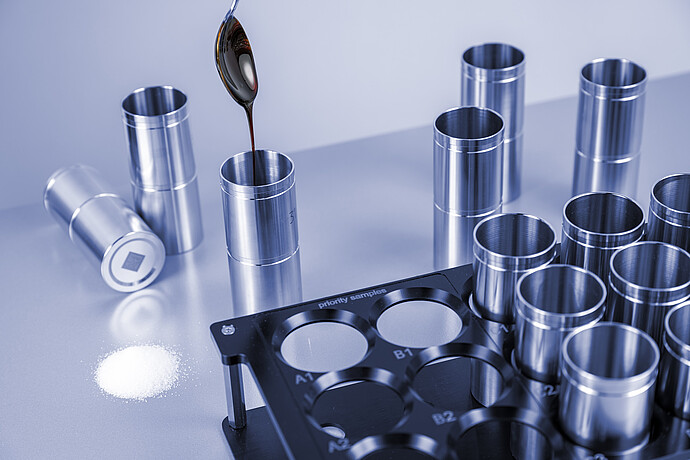
Flexible to adapt to your workflows
Samples from different stages of the sugar production process have different requirements. The Sugarlyzer 5000 offers customers the option to choose from different modules. Whether your sample needs dosing, mixing or filtering, this all-in-solution handles your sample at every step of the way.
Digital job management in combination with automation ensures that every sample is treated according to pre-defined standard operating procedures (SOPs). This enables repeatability and consistency throughout the process. The customer can define how a sample is run (neat, diluted, filtered), and the Sugarlzyer allows the customization of clarification chemistries, mixing times, as well as the temperature during sample preparation.
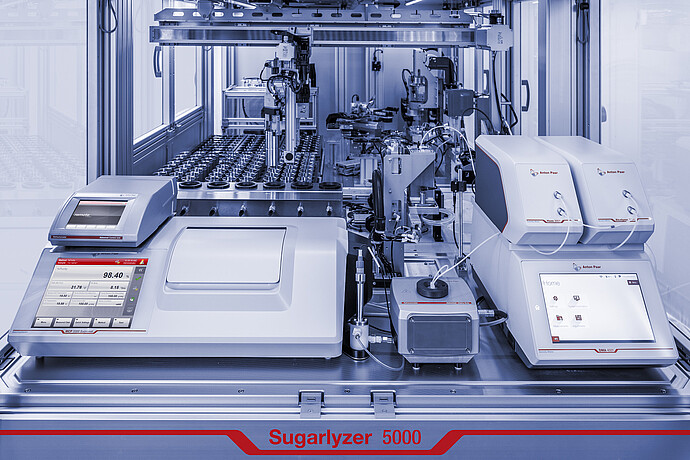
Quality control results you can rely on
Thanks to the sample processing unit (SPU), users are ensured the fast, precise, and simultaneous provision of samples to all instruments, facilitating consistent and accurate results across the board. There is no need to intervene with the sample during or after preparation, therefore minimizing human error and the risk of contamination.
Enjoy the versatility of the SPU, which combines all the instruments needed for sugar analysis, into a comprehensive, all-in-one solution.
Technical specifications
Measuring range | |
Temperature control and measurement | 20 °C |
Sugar content (°Z) at 589 nm | ± 259 °Z (± 89.9 °OR) |
Dry substance (°Brix) | 1.26 - 1.72 nD |
Turbidity [1] | 0 EBC to 100 EBC / 0 NTU to 400 NTU |
Color [1] | 0 EBC to 120 EBC |
Density | 0 g/cm³ to 3 g/cm³ |
pH value | pH 0 to pH 14 |
Repeatability s.d. | |
Temperature control and measurement | ± 0.1 °C |
Sugar content (°Z) at 589 nm | ± 0.003 °OR; ± 0.01 °Z" |
Dry substance (°Brix) | ± 0.000001 nD |
Turbidity [1] | 0.02 EBC / 0.08 NTU |
Color [1] | 0.1 EBC |
Density | 0.000005 g/cm³ |
pH value | 0.02 (in the range pH 3 to pH 7) |
Sample loading capacity | 72 sample cups |
Typical cycle time per sample | approx. 5 min. |
Sample preparation | |
Dosing accuracy (DI water and clearifying agent) | 0.04 ml or 1 % |
Mixing speed | 0 rpm to 2,000 rpm |
Sample pre-tempering station | 65 °C |
Sample volume required | 90 ml to 150 ml / cup |
Environmental conditions | |
Ambient temperature | 22 °C (min. 20 °C, max. 25 °C) |
Relative humidity (not condensing) | at 15 °C to 30 °C: 0 % - 70 %, (non-condensing) |
Tested sample types [2] | |
Sample types | raw juice, thin juice, thick juice, syrup, molasses, sugar |
Further details | |
Pressurized air | ISO 8573-1:2010 [7:4:4], Particle: Class 6, Water: Class 4, Oil: Class 3, Pressure 6 - 10 bar, Pipe diameter Ø 12 mm |
DI water hot | 4 bar to 6 bar abs., chlorine-free (55 °C to 60 °C) 10 L/min |
DI water cold | 2 bar to 4 bar abs., chlorine-free (Room temperature; approx. 20 °C ± 1 %) 1 L/min |
Communication interface | Export of results via CSV-files or bidirectional connection to a LIMS system |
Power supply | 1 x 230 V 50 Hz to 60 Hz 16 A |
Dimensions (L x W x H) (without signal lights and ventilation) | 3,300 mm x 1,600 mm x 2,300 mm |
Distance from the nearest wall | 900 mm |
Weight | Approx. 2,300 kg (5,071 lbs) |
Altitude | Max. 2,000 m (max. 6,560 ft) |
Ventilation (connection to suction line from customer) | 200 m³/h |
Air consumption | 300 L/min; peak 800 L/min |
Sound pressure | Weighted average sound pressure level La = 62 dB(A), short term below 85 dB(A) |
Display | Industrial-PC 1,920 px x 1,080 px |
Controls | Mouse + Keyboard |
[1] Other parameters and units on request.
[2] Approval for other sample types on request.
Anton Paar Certified Service
- More than 350 manufacturer-certified technical experts worldwide
- Qualified support in your local language
- Protection for your investment throughout its lifecycle
- 3-year warranty
Documents
-
Brochure_Sugarlyzer 5000 Brochures