Optimizing Polymer Processing
Struggling with material inconsistencies, inefficiencies, or sustainability challenges? Discover how our advanced polymer processing solutions optimize workflows and enhance product quality.
Plastics are essential in industries like automotive, healthcare, and packaging due to their versatility and durability. However, sustainability concerns drive innovation. To reduce waste and improve recyclability, companies rely on plastics analytics to optimize materials, refine processes, and ensure product quality – enhancing efficiency and sustainability.
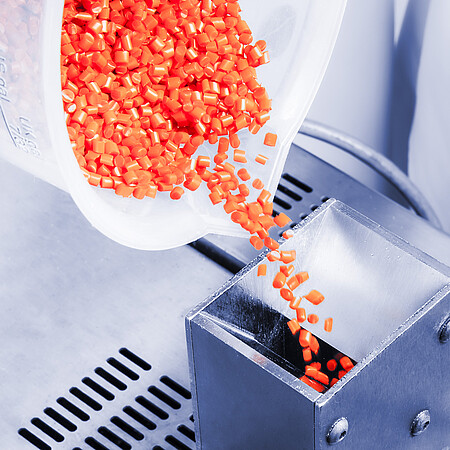
Understanding Polymer Processing
Key methods in polymer processing and mass processing in plastics technology include injection molding, extrusion, blow molding, thermoforming, rotational molding, and 3D printing.
This page and our e-book focus on flat film extrusion, covering the following process steps:
- Raw material preparation ↓
- Recipe development ↓
- Compounding and extrusion ↓
- Film production and molding ↓
- Quality control in final products ↓
- Recycling and sustainability ↓
Plastic film extrusion is a highly complex polymer processing method that requires precise process control, extensive material knowledge, and cutting-edge technology. The selection of the polymer alone significantly affects the final properties of the film. To achieve the desired mechanical, optical, and barrier properties, it is essential to consider aspects such as viscosity, melting behavior, and the use of additives. The extrusion process itself involves precise temperature and pressure control, ensuring uniform film thickness and structural integrity.
Anton Paar’s extensive instrument portfolio seamlessly combines polymer processing technology with plastics analytics, all available from one source. It covers processes from mixing, single-screw extrusion, twin-screw extrusion, to FTIR and Raman spectroscopy, moisture analysis, rheometry, microwave digestion, nanoindentation, zeta potential analysis, gas pycnometry, and viscometry.
Download your free e-book on polymer processing
Your comprehensive guide through the polymer production process of plastic film extrusion, combined with analysis techniques used alongside this process to maximize material performance. This e-book offers production insights and real measurement data and explains how manufacturers enhance efficiency while improving their product’s quality.
Polymer Processing Solutions: Optimizing Every Step
Modern polymer processing is a highly intricate, multi-step workflow that requires precise control at every stage — from raw material selection to final product testing. Variability in polymers, additives, processing conditions, and quality requirements presents significant challenges for manufacturers. Even minor deviations can lead to material waste, production inefficiencies, and costly product defects.
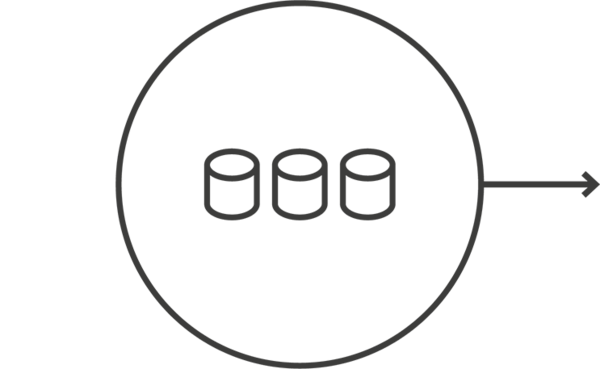
FTIR Spectroscopy
Raman Spectroscopy
Rheological Analysis
Moisture Analysis
Microwave Digestion
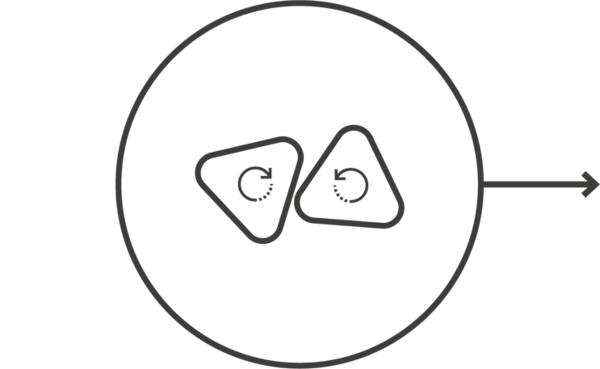
Lab-Scale Mixing
FTIR Spectroscopy
Rheological Analysis
Twin-Screw Extrusion

Twin-Screw Extrusion
Rheological Analysis
Raman Spectroscopy
Gas Pycnometry
Dilute Viscometry
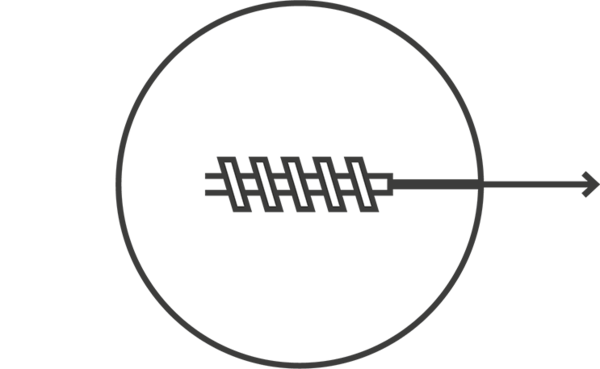
Single-Screw Extrusion
Raman Spectroscopy
Rheological Analysis
FTIR Spectroscopy
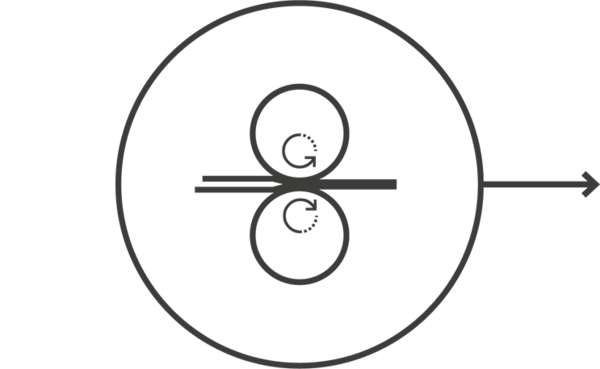
FTIR Spectroscopy
Zeta Potential Analysis
Nanoindentation Testing
Rheological Analysis
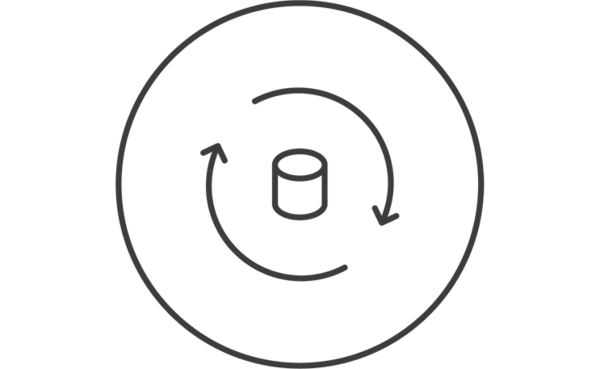
FTIR Spectroscopy
Dilute Viscometry
Microwave Digestion
Anton Paar offers comprehensive solutions that integrate seamlessly into every stage of polymer processing, ensuring optimal material performance, enhanced process efficiency, and improved product quality.
Below, we explore key processing challenges and the solutions that empower polymer manufacturers to achieve superior results.
Ensure Consistent Quality Standards for Raw Materials

Challenge:
Variability in raw materials can lead to inconsistent processing, product defects, and increased waste levels. Contaminants, moisture content, and fluctuations in polymer composition can alter processing conditions, ultimately impacting mechanical properties and overall product quality.
Solution:
Ensure raw material quality and consistency through advanced polymer analysis.
Methods and Instrumentation:
- Material Identification & Purity Analysis: Quickly verify polymer identity, crystal structure and detect contamination.
- Rheological Behavior Assessment: Helps optimize processing parameters by measuring viscosity and elasticity.
- Moisture Content Control: Ensures precise drying time prediction and eliminates processing issues caused by excessive moisture.
- Sample Preparation for Elemental Impurity Detection: Identifies trace elements that affect product stability and durability.
Choose the perfect product combination:
This powerful combination directly addresses the two most critical challenges in maintaining consistent quality standards for raw materials – moisture control and material purity – ensuring stable processing, consistent product quality, and reduced waste. Aquatrac-V eliminates moisture-related defects at the source, while Lyza 7000 ensures precise chemical composition with advanced FTIR analysis, giving you complete confidence in your raw materials.
Recipe Development: Fine-Tuning Polymer Formulations

Challenge:
The development of an optimized polymer formulation requires careful balancing of polymer blends, additives, and fillers. Inaccurate formulations can lead to processing difficulties, material waste, and suboptimal product performance.
Solution:
Achieve precise formulation control and repeatability.
Methods and Instrumentation:
- Small-Scale Batch Testing: Enables reproducible formulation development under controlled conditions.
- Chemical Composition Verification: Ensures accurate polymer and additive quantification, including fast measurements of additives like CaCO₃.
- Process Optimization & Flow Behavior Analysis: Measures formulation impact on material flow properties and end-use performance.
Choose the perfect product combination:
This powerful combination tackles the two key challenges in polymer formulation – material consistency and process optimization – ensuring stable production and reliable performance. Laboratory mixers enable precise blending, twin-screw extrusion with viscometry simulates real processing conditions, and rheometry fine-tunes formulations for consistency. Together, they streamline development, enhance efficiency, and accelerate time-to-market.
Compounding & Extrusion: Optimizing Material Processing

Challenge:
Ensuring homogeneous blending of polymers, additives, and fillers is critical for producing materials with consistent properties. Any variability in the extrusion process can lead to mechanical failure, inconsistent textures, or defects, if not detected on time by suitable analytics.
Solution:
Optimize material properties through real-time monitoring and process adjustments.
Methods and Instrumentation:
- Material Blending & Extrusion: Ensures uniform dispersion of polymers, additives, and fillers during processing.
- Density & Porosity Characterization: Ensures uniform polymer blending and accurate datasheet specifications.
- Real-Time Polymer Composition Analysis: Enables in-line monitoring for material composition control.
- Process Rheology & Extrusion Optimization: Provides precise data for optimizing extrusion, material flow, and processing parameters.
- Fast quality control: PBT grade determination
Choose the perfect product combination:
This powerful combination ensures precise polymer blending and real-time composition control – key to achieving consistent material properties and regulatory compliance. Accurate dosing and mixing prevent quality issues, while in-situ Raman spectroscopy enables real-time quantification, minimizing reliance on offline analysis. Together, they shorten development cycles, allow immediate adjustments, and streamline process optimization.
- Application Report: Combining Extrusion and Raman Spectroscopy: Monitoring Crystallization of a Polymer in Real-Time
- Application Report: Combining Extrusion and Raman Spectroscopy: Monitoring LDPE Phase Transitions In-Line
- Application Report: Combining Extrusion and Raman Spectroscopy: Monitoring Concentrations of a Polymer Blend in Real-Time
Single-Screw Extrusion & Film Production

Challenge:
Achieving consistent film thickness, transparency, and mechanical strength is critical to meet industry requirements. Insufficient control can result in variable material properties, increased waste, and compromised performance.
Solution:
Maintain film quality and process stability.
Methods and Instrumentation:
- Material Melting & Shaping: Ensures optimal extrusion conditions for film production.
- Automated Film Defect Detection: Detects defects in real time to improve process control.
- Crystallinity & Structural Integrity Analysis: Provides insights into polymer crystallinity and composition consistency.
- Processing Parameter Optimization: Ensures proper film structure and performance.
- Real-Time Molecular Insights & Quality Control: Monitors melting and crystallization for improved consistency and process control.
Choose the perfect product combination:
This powerful combination delivers real-time insights into both mechanical and chemical properties, ensuring precise control over melting, crystallization, and material behavior. By integrating rheometry and Raman spectroscopy, you gain a complete picture of polymer transformations under real processing conditions. This accelerates development, enhances quality control, and enables data-driven decision-making – minimizing trial-and-error and optimizing material performance.
Final Product Quality Control

Challenge:
Ensuring that finished plastic films comply with industry standards for mechanical durability, optical clarity, and chemical resistance requires precise characterization methods.
Solution:
Implement advanced testing methods for precise quality control.
Methods and Instrumentation:
- Material Authentication & Consistency: Verifies polymer composition and purity.
- Process Parameter Optimization: Enhances mechanical and chemical performance through surface and bulk analysis.
- Mechanical Strength Evaluation: Assesses material hardness and durability.
- Surface & Particle Analysis: Ensures modifications meet quality and performance requirements.
Choose the perfect product combination:
This powerful combination provides critical insights into surface chemistry and mechanical integrity, ensuring high-performance polymer films and advanced materials. Zeta potential analysis optimizes surface modifications, while nanoindentation testing evaluates hardness and durability at the micro- and nanoscale. Together, they enhance material characterization, improve reliability, and support advanced manufacturing processes.
Recycling & Sustainable Polymer Processing

Challenge:
Recycled plastics frequently contain contaminants, degraded polymers, and variable molecular weights, which can affect processability and product quality.
Solution:
Improve recycled polymer quality.
Methods and Instrumentation:
- Polymer Identity & Purity Verification: Ensures accurate classification of recycled materials.
- Sample Preparation for Impurity Detection & Process Optimization: Identifies and quantifies contamination levels in recycled polymers, enabling better process control.
- Suitability: Check of recycled polymers for the intended application.
Achieve optimal polymer processing through comprehensive material insights. Visit our
Polymer Characterization page to learn how expert testing drives superior outcomes.
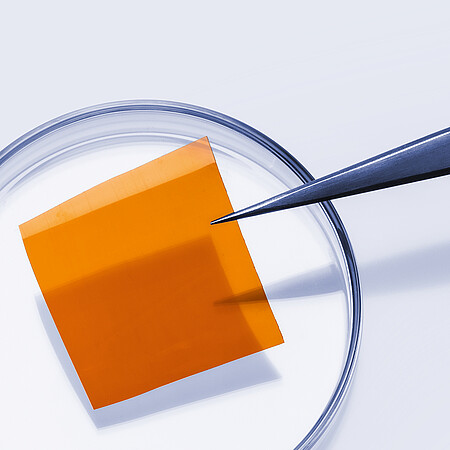
Importance of Polymer Processing Across Industries
Polymer processing is fundamental to modern manufacturing, enabling industries such as automotive, healthcare, packaging, construction, and consumer goods to produce innovative and high-performance products. The process transforms raw plastic materials into functional items through specialized techniques.
Why Plastics?
Plastics deliver unparalleled versatility, lightweight durability, and cost-efficiency, making them indispensable across various applications:
- Automotive: Lightweight polymers help reduce fuel consumption and enhance vehicle safety.
- Healthcare: Biocompatible plastics are essential for medical tubing, implants, and sterile packaging.
- Packaging: Flexible films and rigid containers are crucial for food preservation and product protection.
- Construction: Weather-resistant plastics improve the performance of piping, insulation, and structural materials.
- Consumer Goods: High-performance plastics are key components in electronics, sport equipment, and home appliances.
However, rising sustainability concerns and stricter regulatory requirements are reshaping the industry. To meet evolving environmental standards and customer demands, companies must innovate in plastic formulation, processing, and recycling.
Thermoplastics vs. Thermosets: Understanding the Material Landscape
Distinct plastic types fulfill specialized roles across various industries:
Plastic Type | Properties | Common Applications |
Polyethylene (PE) | Flexible, moisture-resistant | Plastic bags, bottles, film wraps |
Polypropylene (PP) | Chemical-resistant, durable | Automotive parts, medical devices, food containers |
Polyvinyl Chloride (PVC) | Rigid or flexible, weather-resistant | Pipes, medical tubing, window frames |
Polystyrene (PS) | Lightweight, insulating | Packaging foam, disposable cups, insulation |
Polyethylene Terephthalate (PET) | Transparent, strong | Beverage bottles, food packaging, textiles |
Epoxy Resins (Thermoset) | Strong, heat-resistant | Aerospace components, adhesives, coatings |
Polyurethane (PU) (Thermoset) | Elastic, shock-absorbing | Foam insulation, furniture, footwear |
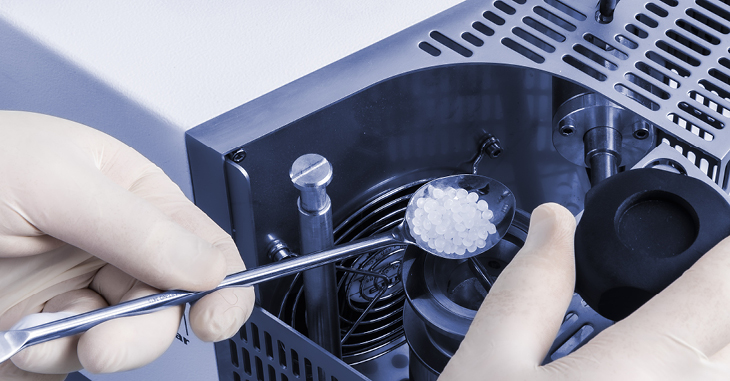
Industry Challenges and the Need for Precision Processing
Different polymer types demand tailored processing conditions to achieve the desired mechanical, optical, and barrier properties. Factors such as viscosity, melting behavior, and precise additive control significantly impact the final product’s performance.
To ensure optimal processing conditions and product consistency, manufacturers depend on advanced analytical techniques for accurate measurement and control.
Sustainability and Regulatory Challenges in Polymer Processing
The plastics industry is confronted with growing challenges in waste management, energy efficiency, and regulatory compliance. Recycling initiatives and energy-saving technologies promote a circular economy, while stricter global regulations demand more sustainable practices.
In this context, plastic analytics plays a crucial role in optimizing material selection, processing, and quality control -enabling manufacturers to efficiently meet both sustainability goals and regulatory standards.
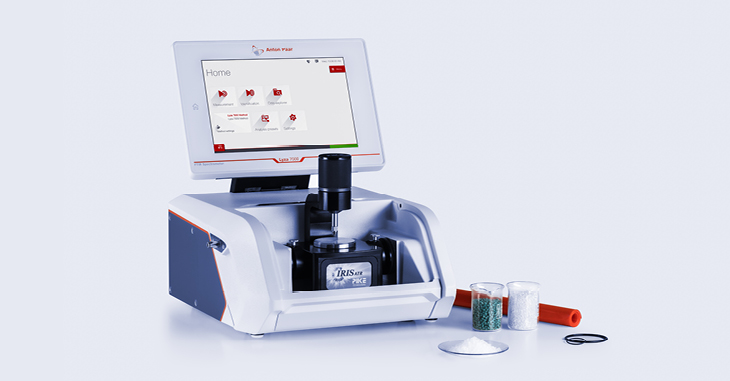
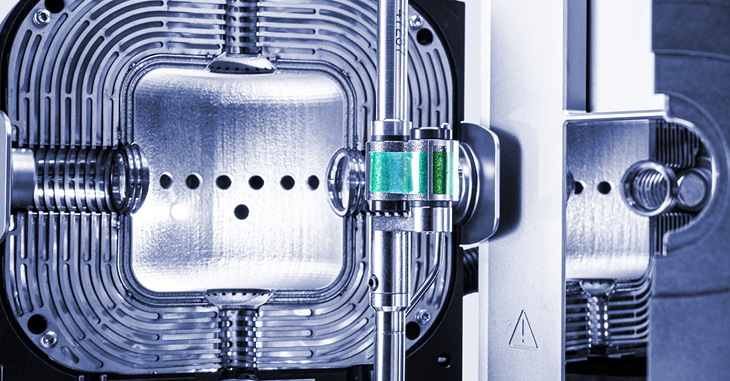
Optimizing Polymer Processing with Advanced Analytics
Manufacturers face numerous challenges in polymer selection, process control, and final product quality. Anton Paar addresses these challenges with cutting-edge measurement solutions that:
- Precisely characterize raw materials to ensure consistency and purity.
- Optimize formulation and processing conditions through real-time data insights.
- Enhance quality control to comply with industry standards and regulatory requirements.
- Improve sustainability by evaluating recyclability and material efficiency.
Polymer Processing FAQ
Which process bonds monomers into polymers?
Polymerization is the process that bonds monomers into polymers, typically through addition or condensation reactions.
Polymerization is the chemical process where small molecules (monomers) link together to form long polymer chains. This can occur through two primary mechanisms: addition polymerization, where monomers combine without generating byproducts, or condensation polymerization, which releases small molecules such as water. This reaction is fundamental for producing plastics like polyethylene (PE), polypropylene (PP), and polyvinyl chloride (PVC).
Which process breaks polymers into monomers?
Depolymerization or chemical recycling breaks polymers down into their monomer components.
Depolymerization is the reverse of polymerization, breaking long polymer chains back into their original monomers. This can occur through chemical recycling, pyrolysis, or enzymatic breakdown. It plays a crucial role in plastic recycling and sustainable material recovery by enabling the reuse of monomers in new polymer production.
What is polymer processing?
Polymer processing refers to the techniques used to shape and form polymers into final products, including extrusion, injection molding, and thermoforming.
Polymer processing includes various manufacturing methods that transform raw polymers into functional materials and products. Common techniques include extrusion for films and pipes, injection molding for complex shapes, and blow molding for hollow containers. Controlling viscosity, temperature, and pressure is essential for ensuring material consistency and product quality across industries like automotive, healthcare, and packaging.
Contact us today to benefit from cutting-edge polymer analytics that drive precision, efficiency, and sustainable outcomes.