Multiparameter Measurement System:
Packaged Soft Drink Measurement System
- For regular and diet drinks, energy drinks, and carbonated water
- Simultaneous determination of °Brix, % Diet, CO₂, and O₂ content
- Rapid results: More than 6x quicker than conventional methods
- Modular setup with 10+ industry-specific parameters
- Finished package analysis with zero operator influence
Get results for °Brix and CO₂ content in three minutes and for % Diet in six minutes – up to 6x faster than conventional methods. The Packaged Soft Drink Measurement System combines up to four instruments to determine all quality parameters for regular, mid-calorie, and diet soft drinks as well as (diet) energy drinks and carbonated bottled water in one go. There is zero preparation or intermittent cleaning required, saving you up to two hours a day. This fast quality control for soft drinks helps you optimize your blending process, ensures ideal carbonation levels, and guarantees confidence in the final bottled product.
Included products
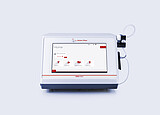
DMA 5002
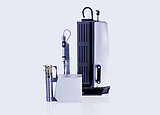
CarboQC ME
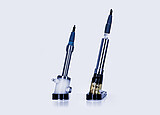
pH 3201
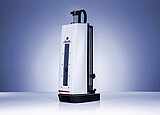
PFD Plus
Key features
All quality control tests for soft drinks in one go
Determine % Diet, °Brix, and CO₂ concentration in regular, mid-calorie, and diet soft drinks, energy drinks, and carbonated water in a single measuring cycle. By reducing the need for reference analysis of diet products to an absolute minimum, you can free up lab capacity while safeguarding product quality and eliminating out-of-spec production.
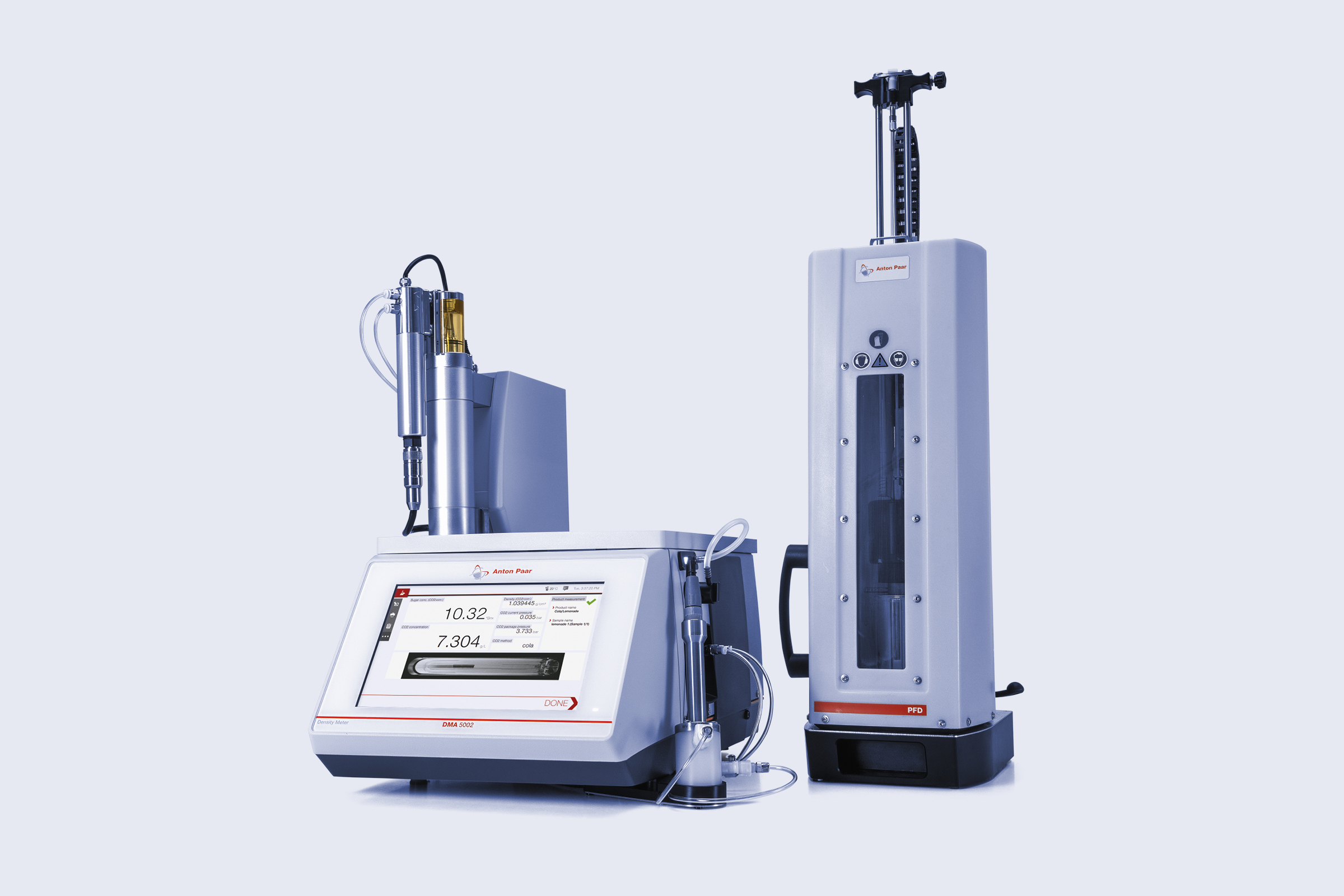
Speed up soft drink quality control by 600 %
The Packaged Soft Drink Measurement Systems provide parallel analysis for all parameters in only three to six minutes (depending on system configuration) – more than 6x faster than conventional methods.
With automatic pressurized filling directly from glass bottles, PET bottles, and cans, no degassing or filtration is required, saving up to seven minutes per sample, while automatic CO₂ correction ensures reliable results. The software-guided adjustment procedure lets anyone manage quality control of diet products and a 360° status light shows measurement progress at a glance – even from a distance.
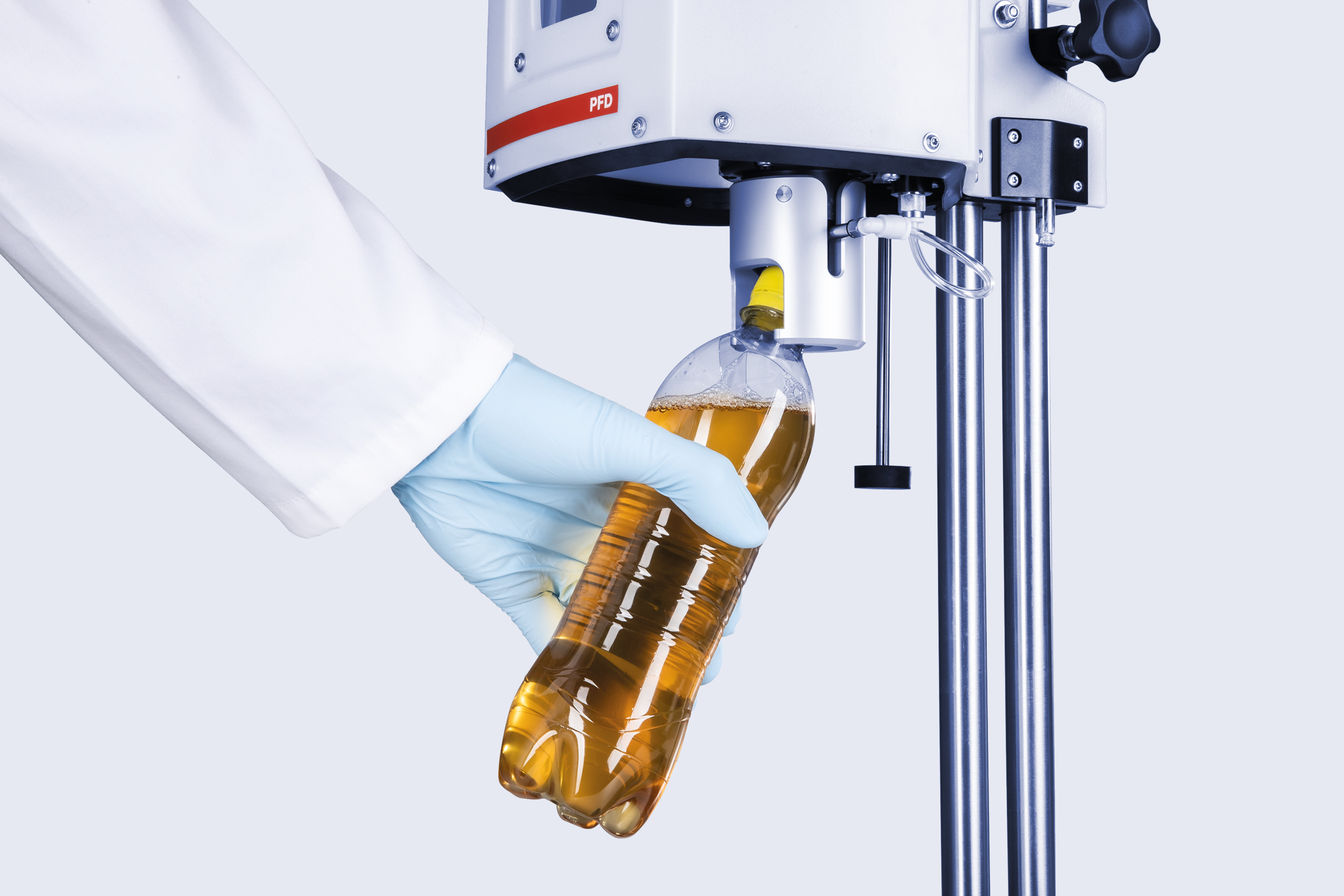
Set up your individual measurement system
The Packaged Soft Drink Measurement System determines the most important soft drink parameters – °Brix / % Diet, CO₂ concentration, and density. Incorporating DMA 6002 Sound Velocity into your measurement system also enables you to precisely monitor the sugar inversion process. To perfect your analysis, upgrade your basic system with modular extensions for measurement of dissolved O₂ and pH. With every module added, you achieve greater system efficiency and increase confidence in your final product quality.
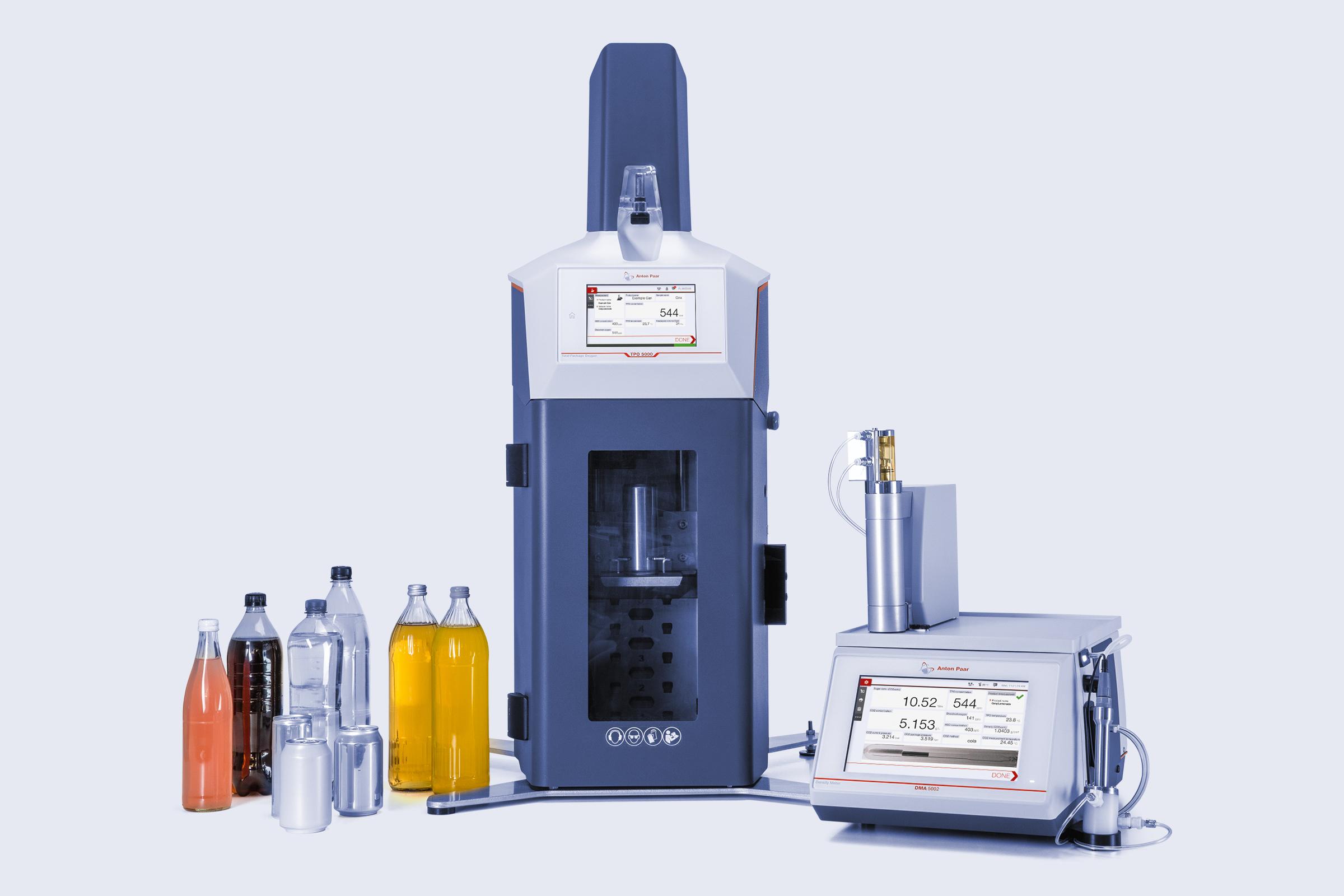
Determine the true amount of dissolved CO₂ in soft drinks
Thanks to a unique selective CO₂ measuring method, the Packaged Soft Drink Measurement System delivers repeatability of 0.005 vol – with no influence from other dissolved gases such as air or nitrogen. Automatic filling error detection in both the density and CO₂ measuring cell leaves no chance for errors.
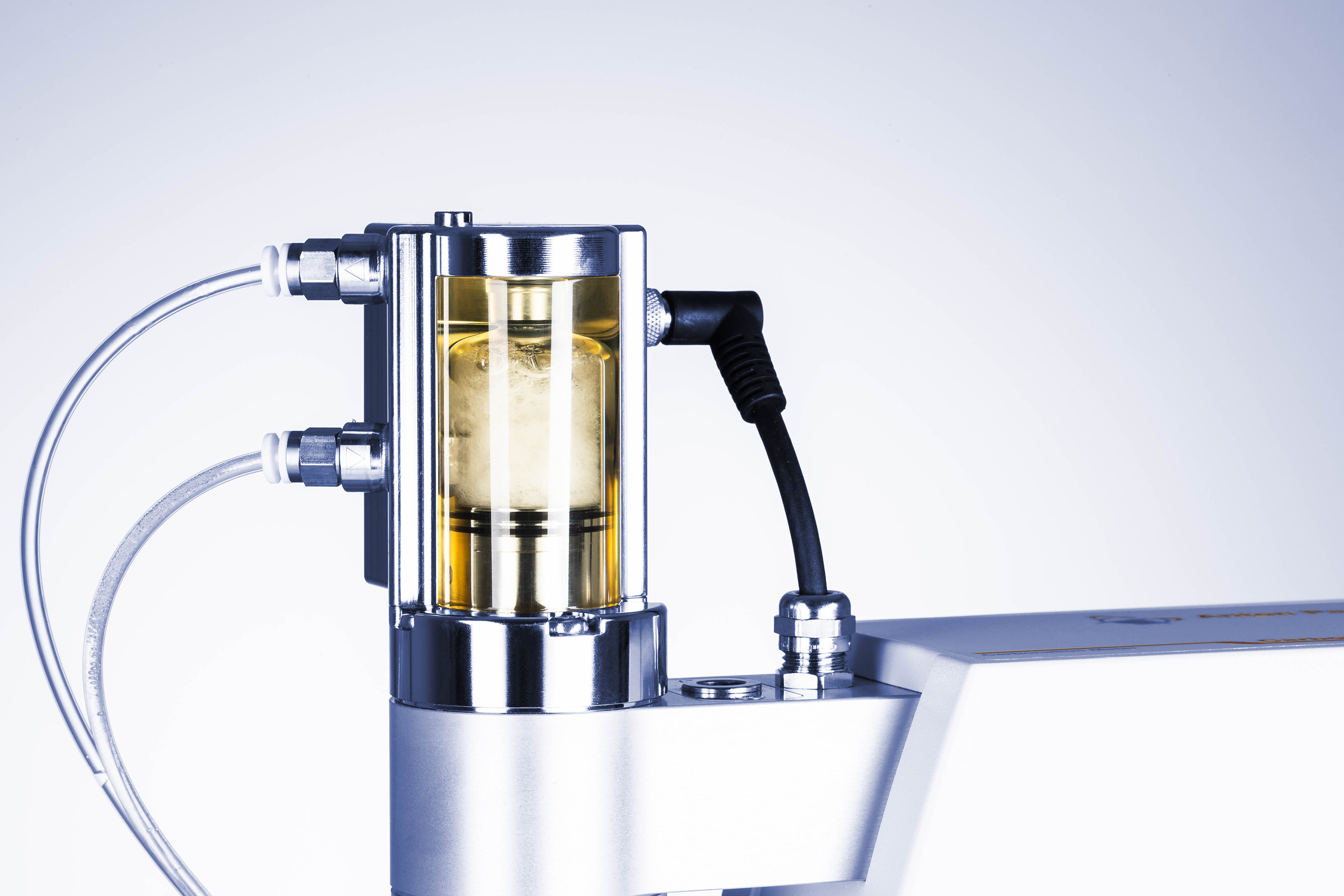
Intuitive usability for maximum convenience
Start your measurement with the push of a button using One-Touch Operation and simultaneously operate each connected measuring module via a single user interface. Built-in wizards guide operators through measuring and adjustment steps, while a wide range of preconfigured output quantities and an adaptable interface ensure maximum operator convenience. Centralized data management is enabled thanks to the AP Connect lab execution software and inline sensors can be adjusted automatically using the Davis 5 software – eliminating the need for manual interaction.
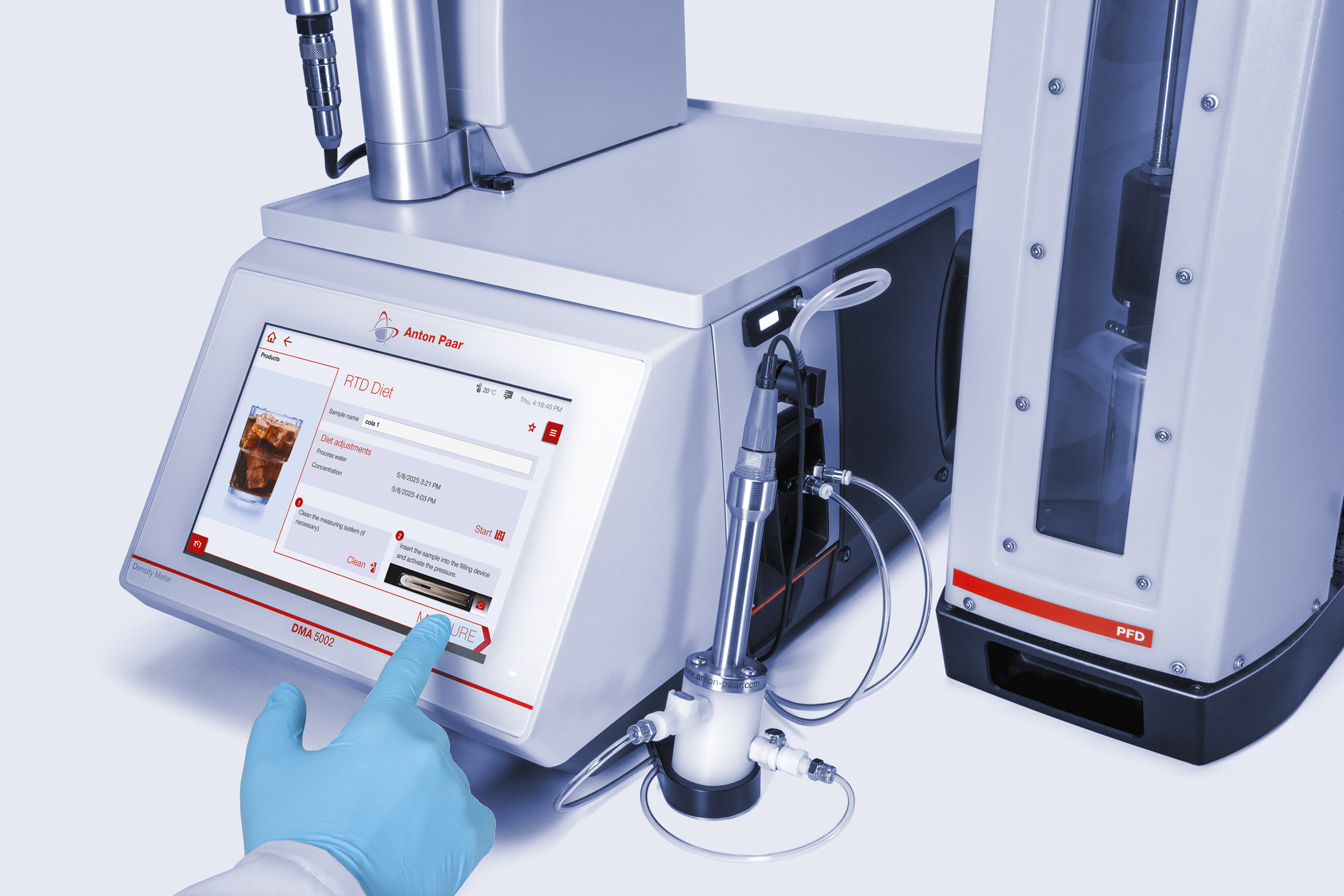
Soft drink quality control including TPO analysis
Achieve premium final quality control for carbonated beverages with the industry’s only integrated solution for total package oxygen (TPO) analysis and over 10 soft drink-specific parameters – all from a single system. Enjoy a seamless measurement experience across all packaging types, including glass bottles, PET bottles, and cans. Our selective TPO measurement principle helps safeguard product shelf life and prevent losses due to can corrosion. Benefit from effortless one-click instrument cleaning and a high level of software automation that boosts efficiency and frees up operator time.
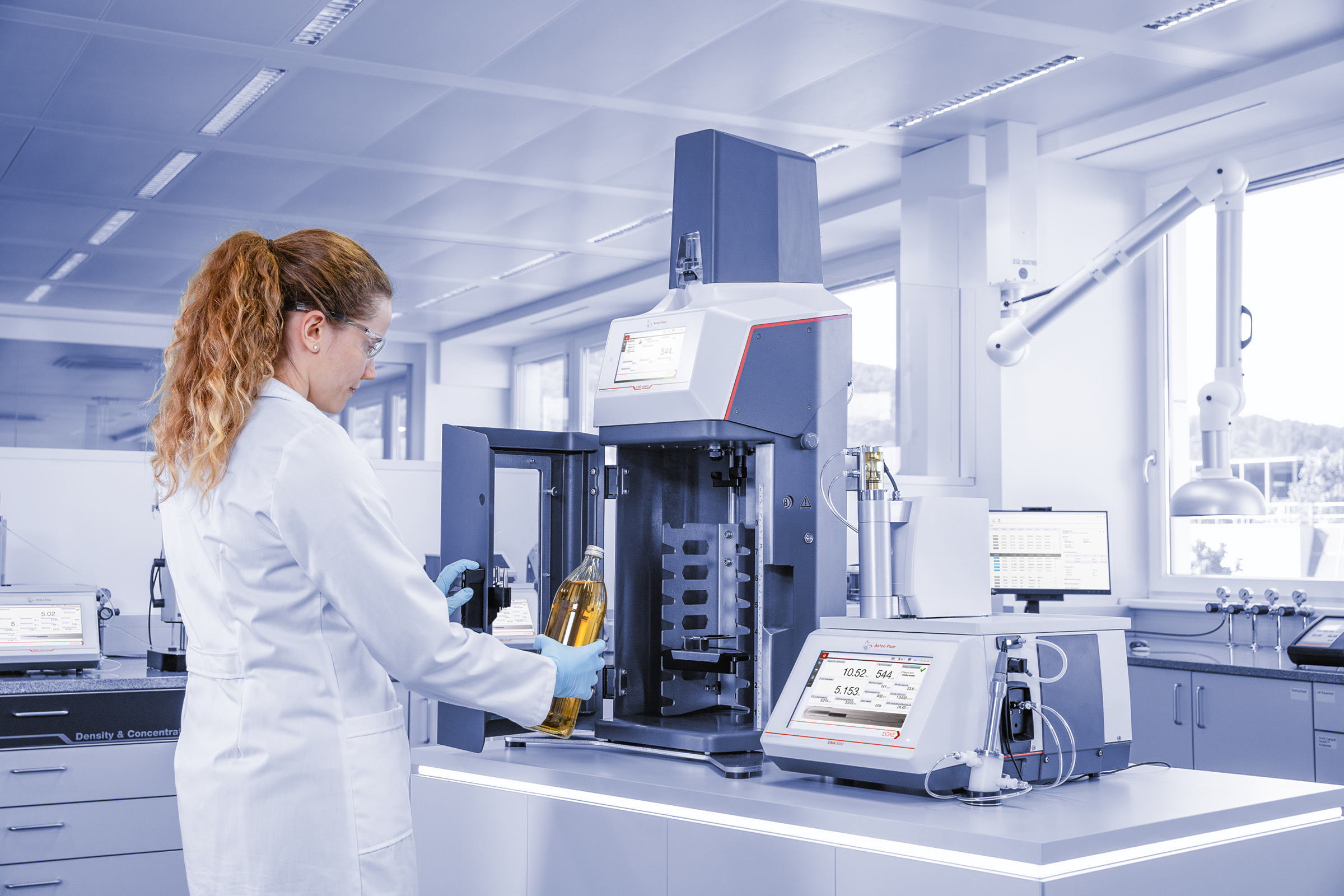
Anton Paar Certified Service
- More than 350 manufacturer-certified technical experts worldwide
- Qualified support in your local language
- Protection for your investment throughout its lifecycle
- 3-year warranty
Documents
-
PBA 5001 Soft Drink Diet | SOP Manuals
-
PBA 5001 Soft Drink | SOP Manuals